Pipelines werden für den Transport zu Erdgasverbrauchern gebaut. Entwerfen Sie ihre Designorganisationen, die eine Lizenz zur Ausführung solcher Arbeiten erhalten haben. Für die Installation von Gasleitungen werden Rohre verschiedener Stahlsorten verwendet verschiedene Wege (bei unterschiedlichen Temperaturen und Drücken). Je nach Produktionsmethode können Stahlrohre für Gas in nahtlose (warmgeformte und kaltgeformte) und geschweißte (mit einer geraden und spiralförmigen Naht) unterteilt werden.
Stahl für die Herstellung von Produkten dieses Typs muss GOST 380 88 entsprechen. Technische Eigenschaften GOST 1050 88 regelt. Die Dicke der Rohre wird durch Berechnungen bestimmt, da für eine unterirdische Rohrleitung mindestens 3 mm und für Überlandrohrleitungen mindestens 2 mm betragen sollten. Die Gasleitung muss zertifiziert sein. In den Unterlagen müssen Hersteller, GOST, Stahlsorte, Produktionsmethode, Prüfinformationen, Chargennummer und Qualitätskontrollzeichen für die Einhaltung angegeben sein.
Anwendungsbereiche von Stahlrohren für Gasleitungen:
- - in Gasversorgungssystemen mit einem Druck von bis zu 1,6 MPa - Wasser- und Gasleitungen (GOST 3262-75) mit einer Nennbohrung von bis zu 80 mm;
- - in Gasleitungen mit unterschiedlichen Drücken - nahtlose Stahlrohre (GOST 8734-75 und GOST 8732-78), die einem Druck von bis zu 10 MPa standhalten;
- - in Gasleitungen mit hohem Druck - längsgeschweißte Rohre (GOST 10704-76) mit einem Durchmesser von 30 bis 426 mm und einer Wandstärke von 3 bis 12 mm.
Die Vorteile von Stahlrohren für Gas
Stahlrohre für Gasleitungen:
- - langlebig;
- - beständig gegen Innendruck;
- - Die lineare Ausdehnung von Stahlrohren ist 20-mal geringer als die von Rohren aus Polyethylen.
- - hundertprozentige Gasdichtheit, die ein Austreten von Gas verhindert.
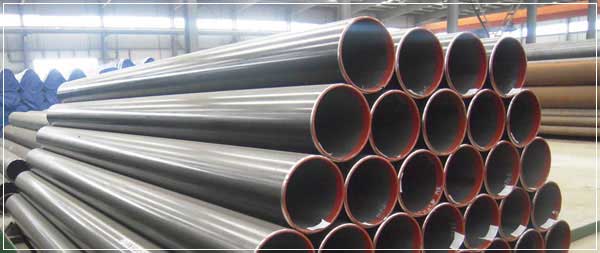
Die Nachteile von Stahlrohren für Gas:
- - Korrosionsneigung, die zu einer Verringerung des inneren Hohlraums führt;
- - relativ großes Gewicht;
- - mühsame und zeitaufwändige Installation;
- - hohe Wärmeleitfähigkeit, die zur Bildung von Kondensat an der Außenfläche führt, wodurch der Korrosionsprozess beginnt;
- - Schweißverbindung - am anfälligsten für Rost;
- - Beschränkungen der Länge der gelieferten Produkte;
- - begrenzte Flexibilität.
Installation der Gasleitung
Gasbedarf:
- - Die Situation sollte vollständig mit dem Projekt übereinstimmen.
- - auf der Gasleitung die Isolierung mit welchem \u200b\u200bStahl gasleitungen;
- - Alle Verbindungen müssen vollständig dicht und nicht dicht sein.
- - Die Rohre müssen fest am Boden anliegen.
- - das Bett sollte aufbewahrt werden;
- - Pflichtelemente sind Wasserabläufe (für die Kondensatableitung von der Außenfläche) und Dehnungsfugen (zur Neutralisierung der linearen Ausdehnung des Rohrs).
Der Graben für die Gasleitung kann nicht im Voraus vorbereitet werden. Sein Boden sollte von Schmutz und Steinen gereinigt werden. Die Gasleitung wird aus separaten Elementen montiert, die außerhalb des Grabens geschweißt sind. Beim Absenken einzelner Elemente in den Graben sind Stöße gegen die Wände oder den Boden nicht zulässig. Wenn die Gasleitung im Winter verlegt wird, sollte der Graben unmittelbar vor dem Verlegen der Elemente in nicht gefrorenen Boden gegraben werden. Auf felsigen Böden ist sandiger Boden (ca. 200 mm) erforderlich.

Isolierung der Außenfläche von Stahlrohren
Wenn die Rohrleitung in den Boden verlegt wird, ist sie Korrosion und Streuströmen ausgesetzt, die ihre Wände zerstören. Um die Lebensdauer von Rohren zu verlängern, werden sie werkseitig mit verschiedenen Korrosionsschutzmaterialien beschichtet. Während des Transports und der Installation sollten Sie vorsichtig mit den Rohren umgehen, da es ziemlich schwierig ist, die Isolierung vor Ort wiederherzustellen.

Während der Installation sind jedoch Arbeiten erforderlich, um die Verbindungen zu isolieren, die nach dem Schweißen einzelner Rohrleitungselemente entstehen. Zu diesem Zweck werden verschiedene Korrosionsschutzbeschichtungen auf Basis von Bitumen und Rollenmaterialien (Kraftpapier oder Polymer) verwendet. Abhängig von den Eigenschaften des Bodens kann die Korrosionsschutzisolierung normal, verstärkt oder sehr verstärkt sein.
Das Rohr wird zu einem metallischen Glanz gereinigt. Dann wird ein Primer darauf aufgetragen. Bitumenmastix wird in Bitumenkesseln hergestellt und mit einer Gießkanne im heißen Zustand auf die Grundierung aufgetragen. Über den Mastix wird eine Rolle Isoliermaterial über den Schoß gewickelt.
Innenisolierung von Stahlrohren
Epoxidmaterialien werden am häufigsten zur inneren Isolierung von Stahlrohren verwendet. Sie verhindern Korrosion der Innenfläche und das Auftreten anderer Ablagerungen und halten den Durchsatz konstant.
Die Rohrleitung für den Gastransport besteht nicht nur aus Stahlrohren, sondern auch aus Hähnen, Hydraulikventilen, Dehnungsfugen und Kondensatfallen. Krane bestehen aus Gusseisen, Stahl und Bronze mit einem Durchmesser von 15 - 700 mm. Die Tore erfüllen die Funktion der Trennvorrichtungen: Um das Gas abzusperren, wird der Rohrleitung Wasser zugeführt, das den unteren Teil des Ventils füllt und den Gasfluss unterbricht. Um das Gas wieder anzuschließen, wird das Wasser durch Spülen entfernt. Festigkeitsprüfungen der Ventile sind im Werk.
Kompensatoren sind in Bohrlöchern montiert und an die Gasleitung angeschlossen. Bei Minustemperaturen werden sie vor der Installation gedehnt und bei positiven Temperaturen komprimiert. Kondensatsammler sammeln Kondensat aus der Gasleitung und werden daher an den unteren Punkten montiert. In regelmäßigen Abständen muss Wasser von diesen Geräten entfernt werden.

Die in Gasversorgungssystemen verwendeten Materialien und technischen Produkte müssen in erster Linie zuverlässig sein und den Anforderungen staatlicher Normen oder technischer Spezifikationen entsprechen, die in der festgelegten Reihenfolge genehmigt und gemäß GOST 2.114–70 * (XXXXXX) staatlich registriert wurden. Traditionell werden Stahlrohre für Gasleitungen verwendet. In den letzten Jahren wurden jedoch zunehmend Rohre aus Polyethylen, Vinyl-Kunststoff und Asbestzement verwendet, insbesondere für den Transport von zugehörigen Gasen mit einem Gehalt von mehr als 3% Schwefelwasserstoff sowie mit sehr hoher Korrosionsaktivität von Böden und in Gegenwart von Streuströmen.
Für unterirdische Inter-Settlement-Gaspipelines mit einem Druck von bis zu 0,6 MPa und unterirdische Gaspipelines mit einem Druck von bis zu 0,3 MPa, die im Siedlungsgebiet verlegt werden, werden Polyethylenrohre gemäß den Sicherheitsregeln des Gosgortekhnadzor der Russischen Föderation PB 12-529-03 verwendet. Es ist auch erlaubt, Gasleitungen von zu verlegen polyethylenrohre Druck von 0,3-0,6 MPa im Gebiet von Siedlungen mit ein-, zweistöckigen und Häuschengebäuden mit einer Bevölkerung von bis zu 200 Einwohnern. Auf dem Territorium von Städten und Industrieunternehmen gesättigt mit Versorgungsunternehmen, Gaspipelines aus metallrohre nicht gebaut.
Zertifikate von Herstellern oder Zertifikate mit einem Auszug aus den Zertifikaten, die bestätigen, dass sie den Anforderungen von Kap. 11 SNiP 2.04.08–87 (XXX). In Ermangelung von Dokumenten werden eine chemische Analyse und eine mechanische Prüfung von Proben durchgeführt, die aus jeder Charge von Rohren derselben Schmelze entnommen wurden, um die Konformität der Qualität mit den aktuellen Anforderungen zu bestätigen. Wenn es nicht möglich ist, die Zugehörigkeit von Rohren zu einer Schmelze festzustellen, sollten Analysen und Tests an Proben aus jedem Rohr durchgeführt werden.
Stahl Röhren. Gemäß den Empfehlungen von SNiP 2.04.08–87 für den Bau von Gasversorgungssystemen werden Rohre aus Kohlenstoffstahl von normaler Qualität gemäß GOST 380-71 oder qualitätsstahl gemäß GOST 1050-74 gut geschweißt und mit nicht mehr als 0,25% Kohlenstoff, 0,056% Schwefel und 0,046% Phosphor.
Stahlrohre werden in 2 Arten hergestellt: geschweißt (gerade und spiralförmig) und nahtlos (warm, heiß oder kalt geformt). Für den Bau von Gaspipelines werden Rohre verwendet, die den Anforderungen von SNiP 2.04.08–87 entsprechen (Tabelle 5.5). Stahlrohre für externe und interne Gasleitungen - Gruppen B und D aus leisem Weichstahl der Gruppe B gemäß GOST 380-71 * nicht niedriger als Kategorie 2 (für Gasleitungen mit einem Durchmesser von mehr als 530 mm und einer Rohrwandstärke von mehr als 5 mm - nicht weniger als 3 Kategorie) der Klassen St2, StZ und St4 mit einem Kohlenstoffgehalt von nicht mehr als 0,25%; Stahlsorten 08, 10, 15, 20 nach GOST 1050-74 *; niedriglegierter Stahl der Sorten 09G2S, 17GS, 17PS gemäß GOST 19281-73 * nicht niedriger als die 6. Kategorie; 10G2 Stahl nach GOST 4543-71 *. In einigen Fällen ist die Verwendung von Rohren aus halb leisem und kochendem Stahl zulässig:
- für unterirdische Gasleitungen in Gebieten mit einer berechneten Außentemperatur von bis zu -30 ° C einschließlich;
- für erhöhte Gasleitungen in Gebieten mit einer Außentemperatur von -10 ° C (aus halb leisem und kochendem Stahl) und -20 ° C einschließlich (aus halb leisem Stahl);
- für interne Gasleitungen mit einem Druck von nicht mehr als 0,3 MPa (3 kgf / cm) 2 ) mit einem Außendurchmesser von nicht mehr als 159 mm und einer Rohrwandstärke von bis zu 5 mm einschließlich, wenn die Temperatur der Rohrwände während des Betriebs nicht unter 0 ° C liegt;
- für externe Gasleitungen Rohre mit einem Durchmesser von nicht mehr als 820 mm (aus halb leisem Stahl) und 530 mm (aus kochendem Stahl) und einer Wandstärke von nicht mehr als 8 mm.
In Gebieten mit einer Außentemperatur von -40 ° C dürfen Rohre aus halb leisem Stahl mit einem Durchmesser von nicht mehr als 325 mm und einer Wandstärke von bis zu 5 mm einschließlich für externe unterirdische Gasleitungen verwendet werden. Für unterirdische und oberirdische Gasleitungen im Freien dürfen Rohre aus halb leisem Stahl und kochendem Stahl mit einem Durchmesser von nicht mehr als verwendet werden 114 mm und Wandstärke bis 4,5 mm.
Für die Herstellung von Biegungen, Verbindungsteilen und Ausgleichsvorrichtungen für Mitteldruckgasleitungen wird nicht empfohlen, Rohre aus halb leisem und kochendem Stahl zu verwenden. Für externe und interne Gasleitungen niedriger Druck, auch für ihre gebogenen Biegungen und Verbindungsteile, ist es zulässig, Rohre der Gruppen A-B aus ruhigem, halb leisem und kochendem Stahl der Klassen St1 gemäß St3 "St4 von 1-3 Kategorien der Gruppen A-B gemäß GOST 380-71 * und zu verwenden 08, 10, 15, 20 gemäß GOST 1050-74.
Für Abschnitte mit Vibrationsbelastungen (die an Vibrationsquellen in Hydraulic Fracturing, Gasverteilungsstationen, Kompressorstationen usw. angeschlossen sind) sollten Stahlrohre der Gruppen B und G aus Weichstahl mit einem Kohlenstoffgehalt von nicht mehr als 0,24% (St2, StZ nicht) verwendet werden weniger als die 3. Kategorie gemäß GOST 380-71, 08, 10, 15 gemäß GOST 1050-74).
Feige. 5.3. Typen schweißverbindungen: a - geschweißte V-förmige Verbindung; b - Schweißverbindung mit einem zylindrischen Unterlegscheibenring; in - eine Schweißverbindung mit einem geformten Unterlegscheibenring. 1 - Gasleitung; 2 - abgeschrägte Rohrkante; 3 - Abstumpfen der Kante; 4 - Schweißnadel; 5 - zylindrischer Unterlagsring;
6 - eine Ringperle; 7 - förmiger Unterlagering.
Rohre, die GOST 3262-75 entsprechen, werden beim Bau von externen und internen Niederdruckgasleitungen mit einem Nenndurchmesser von bis zu 80 mm einschließlich verwendet. Dieselben Rohre der höchsten Qualitätsklasse mit einem Nenndurchmesser von bis zu 32 mm einschließlich sind für gepulste Gasleitungen mit einem Druck von bis zu 0,6 MPa (6 kgf / cm 2) zulässig, während gebogene Abschnitte von gepulsten Gasleitungen einen Schweißradius von mindestens 2Dy und die Rohrwandtemperatur in haben sollten Betriebsdauer - nicht niedriger als 0 ° С.
Nahtlose Rohre (GOST 8731-87 und GOST 8733-87) sind für LPG-Flüssigphasen-Gasleitungen anwendbar, und elektrisch geschweißte Spiralnahtrohre werden für gerade Abschnitte von Gasleitungen verwendet. Darüber hinaus sind Rohre gemäß GOST 8731-87 für die Verwendung bei 100% iger Inspektion von Rohrmetallen durch zerstörungsfreie Verfahren zulässig.
Der Anschluss von Stahlrohren sollte in der Regel durch Schweißen erfolgen. Die Schweißverbindung muss dem Grundmetall der Rohre entsprechen oder einen vom Hersteller garantierten Festigkeitsfaktor aufweisen (gemäß GOST oder TU). Für Niederdruckgasleitungen können Rohre nach GOST 3262-75 * verwendet werden, deren Schweißnähte nicht die Festigkeitseigenschaften der Schweißverbindung aufweisen.
Die Hauptmerkmale der Rohre sind in der Tabelle angegeben. 5.8.
Nichteisenlegierungsrohre. Gepulste Gasleitungen zum Anschluss von Instrumenten- und Automatisierungsgeräten sollten in der Regel aus Stahlrohren für Gasleitungen mit dem entsprechenden Druck bestehen. Für ihre Verbindung dürfen jedoch runde, gezogene, kaltgewalzte Kupferrohre für allgemeine Zwecke gemäß den Anforderungen von GOST 617-72 der Kupfermarken Ml, Mlp, M2, M2r, MZ, MZr gemäß GOST 859-78, Tombaka-Marke L96 gemäß GOST 15527 verwendet werden -70. Der Außendurchmesser dieser Rohre beträgt 3–30 mm, die Wandstärke 0,5–5,0 mm. Erlaubt die Verwendung von gezogenen, kaltgewalzten Messingrohren (Messingqualitäten L63 und L68) für allgemeine Zwecke (GOST 494-76). Gezogene und kaltgewalzte Rohre sind in folgenden Ausführungen erhältlich: weiches M und halbfestes PT (mit entfernten inneren Zugspannungen), Außendurchmesser 3–60 mm, Wandstärke 0,5–5,0 mm.
Es werden gewalzte und gezogene Rohre aus Aluminium AD0, AD1 und Aluminiumlegierungen der Typen AMts, AMg2, AMgZ, AMg5, AMgb, AB, D1, D16 nach GOST 18475-82 verwendet. Je nach Material bestehen die Rohre aus geglühtem M (ADOM, AD1M, AMtsM, AMg2M, AMgZM, AMg5M, AMgbM, AVM, D1M, D16M), gehärtetem und gealtertem T (ABT, D1T, D16T) mit einem Außendurchmesser von 6–120 mm und Wandstärke 0,5–5,0 mm.
Ärmel aus Gummi und Gummi. Beim Betrieb von Installationen mit gas KraftstoffFlexible Gaspipelines sind weit verbreitet: an Gastankstellen (GFS) (beim Ablassen von Gas aus Eisenbahntanks), Abfüllen von Gas mit Tankschiffen, Ablassen von Gas in Gruppentankanlagen und Ersetzen von Flaschen. Gummi und Gummi-Stoffhülsen sorgen für einen kürzeren störungsfreien Betrieb, da sich die physikalischen und mechanischen Eigenschaften von Gummi und Stoff im Laufe der Zeit bis zum Elastizitätsverlust ändern.
Gummi- und Gummischlauchschläuche zur Verwendung in Gasversorgungssystemen sollten gemäß den in der Tabelle aufgeführten Empfehlungen ausgewählt werden. 5.7–5.8. Bei der Auswahl der Schläuche sollte deren Beständigkeit gegenüber dem transportierten Medium bei einer minimalen Betriebstemperatur berücksichtigt werden. Schläuche aller Klassen müssen an jedem Ende spezielle Vorrichtungen unterschiedlicher Bauart für den Anschluss an Rohrleitungen und Armaturen von Behältern und Apparaten aufweisen.
Bei der Bestimmung der Länge der Hülsen sollte die Möglichkeit einer Schrumpfung berücksichtigt werden, die 3-4% der Gesamtlänge der Hülse erreichen kann. Die Enden der Rohre unter der Hülse müssen gerade sein und nicht weniger als den doppelten Durchmesser der Hülse haben
Verbindungen müssen standhalten hydraulischer DruckDer doppelte Arbeitsdruck im System und die Prüfpneumatik entsprechen dem Arbeitsdruck im System.
Polyethylenrohre. Gemäß SNiP 42-01-02 können diese Rohre zur Gasversorgung von Dörfern und ländlichen Siedlungen verwendet werden, die Erdgase aus Gas- und Gasfeldern liefern, die keine aromatischen und chlorierten Kohlenwasserstoffe enthalten. Sie bestehen aus Niederdruckpolyethylen mit der Bezeichnung "GAZ" gemäß TU 6-19-051-538-85. Rohre vom Typ C werden für Nieder- und Mitteldruckgasleitungen verwendet.
Die Verbindung von Polyethylenrohren - Schweißen, abnehmbare Polyethylenrohre mit Stahlrohren, mit Dehnungsfugen und Absperrventilen - an Buchsen für einen Flansch in einem Bohrloch oder bei einteiligen Verbindungen - durch ein Glockenkontaktverfahren im Boden.
Die Tiefe der Polyethylenrohre beträgt mindestens 1 m bis zur Rohroberseite. Standardabstände zu Bauwerken und Gebäuden werden gemäß SNiP 2.07.01-86 übernommen. Die Verwendung von Polyethylenrohren für Gasleitungen ist nicht zulässig:
- in Bereichen mit einer Auslegungstemperatur unter -40 ° C,
- in stark flaumigen, felsigen Böden,
- im Boden Typ II Senkung,
- in Gebieten mit unterminierten Gebieten
- in Gebieten mit Seismizität über 6 Punkte.
Es ist verboten, ober- und unterirdische Gasleitungen aus Polyethylenrohren sowie in Sammlern, Kanälen und in Gebäuden zu verlegen.
Anschlüsse und Armaturen, Einheiten und Teile von Rohren. Für Gasleitungen und gasausrüstung Werksbeschläge und Teile aus Temperguss oder Weichstahl (gegossen, geschmiedet, gestanzt, gebogen oder geschweißt) werden gemäß den staatlichen und industriellen Standards verwendet (Tabelle 7.11).
Die Verwendung der Verbindungsteile und -teile, die unter Berücksichtigung der technischen Anforderungen einer der Normen für das entsprechende Verbindungsteil oder -teil hergestellt und auf der Grundlage von Bauorganisationen hergestellt wurden, ermöglichte die zerstörungsfreie Prüfung von Schweißverbindungen mit zerstörungsfreien Methoden.
Das Material für die Herstellung von Verbindungsteilen und -komponenten sind nahtlose und längsgeschweißte Stahlrohre oder Bleche aus Stahl, deren Metall die in den Absätzen vorgesehenen technischen Anforderungen erfüllt. 11.5–11.12 SNiP 2.04.08-87.
Gasanschlussflansche müssen GOST 12820-80 * und GOST 12821-80 * entsprechen.
1 - Rohr; 2 - Loch für den Bolzen; 3 - Flansch; 4 - schweißen;; 5 - geschweißter Ring; 6 - Schulter.
Für Windungen der Gasleitung normalisierte gebogene Biegungen von nahtlosen Rohren (in Winkeln von 15, 30, 45, 60, 75 und 90 °) mit einem Radius von (3, 4 und 6) D n (für Dy ≤ 400 mm), steil gebogen (45, 60, 90 °) mit einem Radius von (1 ÷ 5) D n (für Dy ≤ 500 mm) oder gebogenen Biegungen - Gewindequadrate aus Temperguss mit Dy< 50 мм.
An externen Gasleitungen werden Flanschverbindungen verwendet, um Ventile, Ventile und andere Armaturen zu installieren. Gewindeanschlüsse werden an Stellen verwendet, an denen Kräne, Stopfen, Kupplungen an Kondensatfallen und Wasserschlössern installiert sind. absperrventile an erhöhten Durchführungen von Niederdruckgasleitungen und Instrumentenanschlüssen. An internen Gasleitungen sind Flansch- und Gewindeanschlüsse nur zum Anschließen von Absperrventilen, Instrumenten und Geräten zulässig. Steckbare Verbindungen sollten zur Inspektion und Reparatur zugänglich sein. Zum gewindeanschlüsse am häufigsten ist zylindrisch rohrgewinde (GOST 6357-81). In einigen Fällen gilt es metrisches Gewinde (GOST 24705-81) oder konisch (GOST 6111-52 *).
Dichtungsmaterialien. Zum Abdichten von Flanschverbindungen sollten Dichtungen aus den in Tabelle 1 aufgeführten Materialien verwendet werden. 5.10. Paronitdichtungen werden mit Zylinderöl imprägniert und mit Graphitpulver beschichtet. Es dürfen Dichtungen aus einem anderen Dichtungsmaterial verwendet werden, die im Vergleich zu den in der Tabelle angegebenen Materialien nicht weniger dicht sind. 5.10 (unter Berücksichtigung der Parameter Medium, Druck und Temperatur). Um den Dichtungen flammhemmende Eigenschaften zu verleihen, können Metallwelldichtungen verwendet werden.
Zum Abdichten von Gewindeverbindungen sollten Sie mit Flachs gekämmte Litzen (GOST 10330-76 **) verwenden, die mit Minium oder Bleiweiß beschichtet sind. fluoroplastisches Dichtmittel in Form eines Klebebands oder einer Schnur.
Für die Montage von Gewindeanschlüssen kann eine werkseitig hergestellte Passpaste verwendet werden. Es wird empfohlen, passende Pasten- und Polymerbänder in der Nähe von Kesseln und Brennern bei Temperaturen über 60 ° C zu verwenden.
Zur Abdichtung der Dichtungen, Gehäuse und Stellen, an denen die Gasleitung durch die Wände und Fundamente von Bauwerken verläuft, wird ein mit Harz oder Bitumen isolierter Hanfstrang verwendet.
Stopfbuchse und Fett. Das Material für die Herstellung der Stopfbuchspackung wird gemäß GOST 5152-84 ausgewählt. Die technischen Eigenschaften der Dichtungen, die in Gasversorgungssystemen am häufigsten verwendet werden, sind in der Tabelle angegeben. 5.11.
Für Reibeinheiten ohne Wasser bei Temperaturen bis zu 115 ° C werden Schmiermittel auf Konstalinbasis verwendet - ein feuerfestes Kunststoffschmiermittel, das aus Erdöl besteht, das mit Natriumsalzen höherer Fettsäuren verdickt ist.
Für Korkventile aus Bronze wird hitzebeständiges Fett der folgenden Zusammensetzung verwendet, Gew .-%: gemahlener Glimmer - 2; Natriumseife - 35 ± 4; Motoröl - 58 ± 5. Für den kurzfristigen Korrosionsschutz von behandelten Metalloberflächen werden feste Öle oder spezielle Konservierungsfette und -pasten verwendet.
Die Reinigung der Metalloberflächen von Korrosion erfolgt mit Kerosin oder Pulver aus 50 g fein gemahlener Seife und 50 g Tripolis (lockeres oder schwach zementiertes feinporiges Opalsedimentgestein, das in trockenen Baumischungen als aktiver Mikrofiller verwendet wird). Teile waschen - mit Flugbenzin, Testbenzin oder Aceton.
Für die Lagerung in einem Lager werden die besten Ergebnisse mit PVK-Kanonenfett (GOST 19537-83) erzielt, das aus mit Petrolatum und Ceresin mit Korrosionsschutzadditiven verdicktem Erdöl oder Konservierungsöl hergestellt wird.
Rohrleitungsabsperrventile. Dieser Name bedeutet eine breite Palette verschiedener Geräte zur Steuerung der Ströme eines Mediums (flüssig, gasförmig, gasförmig, flüssig usw.), das durch Rohrleitungen transportiert wird. Über die Ventile wird die Versorgung ein- und ausgeschaltet, der Druck oder die Richtung der Gas- oder Flüssigkeitsströme geändert, der Flüssigkeitsstand gesteuert und die Entfernung von Gasen und Flüssigkeiten automatisch erfolgt.
Die Hauptteile des Ventils sind eine Verriegelungs- oder Drosselvorrichtung und ein Antrieb. Sie sind in einem geschlossenen Gehäuse eingeschlossen, in dem sich der Verschluss bewegt. Das Gehäuse ist mit Verbindungsenden ausgestattet, mit denen es hermetisch an der Rohrleitung montiert ist. Die Bewegung des Verschlusses innerhalb des Gehäuses relativ zu seinen Sitzen ändert sich hydraulischer Widerstand Die Passage ist eigentlich seine Fläche.
Ein Sattel ist ein Teil der Innenfläche des Gehäuses oder ein Teil, mit dem der Bolzen mit einem geschlossenen Durchgang zusammenpasst. Verstärkungsvorrichtungen je nach Ziel werden genannt:
- verriegelung - für luftdichte Trennung ausgelegt
- teile der Rohrleitung oder Vorrichtung;
- gas - zur präzisen Steuerung des Durchgangsbereichs - hydraulischer Widerstand.
Bewehrungsklassifizierung. Gemäß dem aktuellen GOST 356-80 sind Armaturen und Verbindungsteile von Rohrleitungen durch Bedingungs-, Prüf- und Arbeitsdruck gekennzeichnet. Abhängig vom bedingten Druck kann die Bewehrung in drei Hauptgruppen unterteilt werden:
- niedriger Druck (ru - bis zu 1,0 MPa);
- durchschnittlicher Druck (ru \u003d 1,6 ≤ 6,4 MPa);
- hoher Druck (ru \u003d 6,4 ÷ 40,0 MPa).
Bedingter Druck - ein Parameter, der die Festigkeit der Bewehrung garantiert und sowohl den Arbeitsdruck als auch die Arbeitstemperatur berücksichtigt. Der bedingte Druck entspricht dem für dieses Produkt bei Normaltemperatur zulässigen Arbeitsdruck - mit steigender Temperatur verschlechtern sich die Eigenschaften von Baustoffen. Die für die Armaturen angegebenen Drücke sind immer zu hoch (nur absolut ausgehandelt). Betriebstemperatur - die maximale Dauertemperatur der Arbeitsumgebung ohne Berücksichtigung kurzfristiger Erhöhungen, die durch die technischen Bedingungen zulässig sind. Ein Überschuss von 5% des in der Norm oder im Katalog angegebenen tatsächlichen Arbeitsdrucks ist zulässig.
Bei der Auswahl des Materials der Armaturen für die Gasversorgung sollten die Betriebsbedingungen berücksichtigt werden, d. H. Gasdruck und -temperatur gemäß den Angaben in der Tabelle. 5.14.
Der Hauptgrößenbereich der Armaturen - Nenndurchmesser Dy - Nenninnendurchmesser der Rohrleitung, auf der diese Armatur installiert ist. Verschiedene Arten von Bewehrungen mit demselben bedingten Durchgang können unterschiedliche Strömungsabschnitte aufweisen. Der bedingte Durchgang darf nicht mit der Bohrung im Ventil verwechselt werden, gleichzeitig stimmt die bedingte Ventilbohrung nicht mit dem tatsächlichen Rohrdurchmesser überein.
Rohrverbindungsstücke werden je nach Verwendungszweck in folgende Klassen eingeteilt:
I - Absperrung, um den Fluss des Mediums vollständig abzusperren;
II - Regulieren, Steuern des Drucks oder der Durchflussrate des Mediums durch Ändern des Durchflussbereichs;
III - Sicherheit, gegebenenfalls Bereitstellung einer teilweisen Freisetzung des Mediums oder vollständige Einstellung seiner Versorgung, um einen Druckanstieg zu verhindern, der die Festigkeit des Systems gefährdet, sowie Verhinderung des Rückflusses des Mediums, der aus technologischen Gründen nicht akzeptabel ist;
IV - Tank-, Steuer- und andere Ventile für verschiedene Zwecke.
Jede Klasse wird nach dem Wirkprinzip in zwei Gruppen eingeteilt (Tabelle 5.15), und Klassen und Gruppen werden nach Art der Bewehrung eingeteilt (Tabelle 5.16). Darüber hinaus weist die Bewehrung jedes Typs zusätzliche Eigenschaften für den beabsichtigten Zweck und das Design auf.
Methoden zum Verbinden von Armaturen. Die Hauptmethoden sind Flansch, Kupplung, Zapfen, geschweißt (einteilig). Oft werden Flanschverschraubungen verwendet, deren Vorteile offensichtlich sind: die Möglichkeit der mehrfachen Montage und Demontage an der Rohrleitung, die Zuverlässigkeit der Dichtungsverbindungen und die Möglichkeit ihres Festziehens, große Festigkeit und Eignung für einen weiten Bereich von Drücken und Durchgängen. Zu den Nachteilen gehören die Möglichkeit, das Anziehen und den Verlust der Dichtheit zu lösen, die vergleichende Komplexität der Montage und Demontage, die Größe und das Gewicht.
Für kleine Gussfittings mit Nennbohrungen bis zu 50 mm (insbesondere Gusseisen) werden häufig Kupplungskupplungen verwendet, deren Hauptbereich Nieder- und Mitteldruckfittings sind.
Für kleine Hochdruckarmaturen aus Schmiedeteilen oder Walzprodukten wird eine Achsverbindung mit einem Außengewinde für eine Überwurfmutter verwendet.
Schweißverbindungen sorgen für eine absolute Langzeitdichtheit der Verbindung und reduzieren das Gesamtgewicht von Ventilen und Rohrleitungen. Der Nachteil von Schweißverbindungen ist die Schwierigkeit, die Armaturen zu zerlegen und auszutauschen.
Gängige Ventiltypen. Je nach Art der Bewegung der Absperrelemente werden die Absperrventile in folgende Typen unterteilt (siehe Tabelle 5.17):
- absperrschieber;
- kräne
- ventile
- drehschlösser.
Verriegelungen - Verriegelungsvorrichtungen, die den Durchgang blockieren, indem der Verschluss in eine Richtung senkrecht zur Bewegung des Flusses des transportierten Mediums bewegt wird. Im Vergleich zu anderen Ventiltypen haben Ventile folgende Vorteile:
- unbedeutender hydraulischer Widerstand bei vollständig offenem Durchgang;
- mangel an Strömungen;
- möglichkeit der Anwendung für Überlappung
- hochviskose Medienströme;
- einfache Wartung;
- die Fähigkeit, Medium in jede Richtung zu liefern.
Die allen Ventilkonstruktionen gemeinsamen Nachteile umfassen:
- unfähigkeit, für Umgebungen mit kristallinen Einschlüssen zu verwenden;
- kleiner zulässiger Druckabfall über dem Ventil (im Vergleich zu Ventilen);
- niedrige Verschlusszeit;
- die Möglichkeit, am Ende des Hubs einen Wasserschlag zu bekommen;
- große Höhe;
- schwierigkeiten bei der Reparatur verschlissener Dichtflächen während des Betriebs;
- die Unfähigkeit, eine konstante Schmierung der Dichtflächen des Sitzes und der Ventile zu verwenden.
Beim Schließen der Ventile erfährt das Verriegelungselement keine merkliche Reaktion des Mediums, da es sich senkrecht zur Strömung bewegt, dh nur Reibung überwunden werden muss. Die Dichtflächen der Ventile sind klein und dank dieser bieten die Ventile eine zuverlässige Dichtheit.
Eine Vielzahl von Ventilkonstruktionen kann im Allgemeinen in zwei Typen unterteilt werden: Keil und Parallel. Keilschieber werden wiederum in Absperrschieber mit integrierten, elastischen und zusammengesetzten Keilen und parallele Ventile in Einzelplatten- (Schieber-) und Doppelscheibenventile unterteilt. Bei Ventilen, die für den Betrieb mit hohen Druckabfällen über das Ventil ausgelegt sind, um die Öffnungs- / Schließkräfte zu verringern, wird die gesamte Durchgangsfläche kleiner als die Querschnittsfläche der Einlassrohre (verengter Durchgang).
Je nach Ausführung der Schrauben-Mutter-Systeme gibt es unterschiedliche Absperrschieber mit ausziehbaren und nicht ausziehbaren Spindeln. Letztere sollten Indikatoren für den Entdeckungsgrad haben.
Tor keilschieber hat die Form eines flachen Keils und die Sitze oder Dichtflächen parallel zu den Dichtflächen des Verschlusses stehen in einem Winkel zur Bewegungsrichtung des Verschlusses. Diese Konstruktion gewährleistet die Dichtheit des Durchgangs in der geschlossenen Position und die Unbedeutung der Dichtkraft.
Bei parallelen Ventilen sind die Dichtflächen parallel zueinander und senkrecht zur Strömungsrichtung des Mediums. Die Vorteile von Ventilen dieser Konstruktion sind die einfache Herstellung des Verschlusses (Scheibe oder Schieber), die einfache Montage und Reparatur sowie das Fehlen eines Verklemmens des Verschlusses in der geschlossenen Position. Parallelventile erfordern jedoch erhebliche Schließ- / Öffnungskräfte und zeichnen sich durch starken Verschleiß der Dichtflächen aus.
Die meisten Ventile können in jeder Position an horizontalen und vertikalen Gasleitungen installiert werden, mit Ausnahme der Spindel-Ab-Position. Die Position von Ventilen mit pneumatischen und elektrischen Antrieben ist besonders geregelt.
Krane sind Verriegelungsvorrichtungen, bei denen der bewegliche Teil des Verschlusses (Stopfen) die Form eines Rotationskörpers mit einer Öffnung für den Durchfluss der Strömung hat und sich, wenn die Strömung blockiert ist, um seine Achse dreht.
Abhängig von der Form der Dichtflächen des Ventils werden die Ventile in drei Typen unterteilt: konische, zylindrische (nicht für Gasgeräte verwendet) und Kugelhähne (mit sphärischem Ventil). Darüber hinaus kann die Konstruktion der Krane in anderen Parametern variieren, beispielsweise durch das Verfahren zur Erzeugung von Druck auf die Dichtflächen, durch die Form des Durchgangsfensters, durch die Anzahl der Durchgänge, durch die Art der Steuerung und des Antriebs, durch Baumaterialien usw.
Die Konizität des Stopfens (Körpers) von konischen Kranen wird in Abhängigkeit von den Gleitfähigkeitseigenschaften der verwendeten Materialien eingestellt und beträgt 1: 6 oder 1: 7. Entsprechend der Methode zur Erzeugung eines bestimmten Drucks zwischen dem Körper und dem Stopfen, um die erforderliche Dichtheit im Ventil sicherzustellen, werden die Ventile mit einem konischen Ventil in die folgenden Typen unterteilt: Spannung, Stopfbuchse mit Fett und mit dem Druck des Stopfens.
Die Gruppe der Spannkrane umfasst weit verbreitete Gewindekupplungskupplungskrane, die einfach aufgebaut sind und die Spannkräfte bequem einstellen können. Füllventile zeichnen sich dadurch aus, dass durch Anziehen der Stopfbuchse die für die Dichtheit an den konischen Dichtflächen von Gehäuse und Stopfen erforderlichen spezifischen Drücke erzeugt werden. Die Anziehkraft wird auf den Stecker übertragen und auf den Sattel gedrückt. Geschmierte Stopfbuchsen werden verwendet, um den Kontrollaufwand bei mittleren und großen Durchmessern der Nennbohrung, spezifische Drücke auf die Dichtflächen zu verringern und ein Reißen der Kontaktflächen zu verhindern.
Kugelhähne sind weit verbreitet und bieten alle Vorteile von Kegelventilen (einfache Konstruktion, direkter Durchfluss und geringer hydraulischer Widerstand, Konstanz des gegenseitigen Kontakts der Dichtflächen), die sich gleichzeitig günstig unterscheiden:
- kleinere Abmessungen;
- erhöhte Festigkeit und Steifheit;
- erhöhte Dichtheit aufgrund der Konstruktion (die Kontaktfläche der Dichtflächen des Gehäuses und des Stopfens umgibt den Durchgang vollständig und dichtet den Ventilverschluss ab);
- weniger arbeitsintensive Herstellung (mangelnde arbeitsintensive Bearbeitung und Schleifen der Dichtflächen von Körper und Kork).
Kugelhähne können trotz der Vielfalt der Ausführungen in zwei Haupttypen unterteilt werden: schwimmende Absperrventile und schwimmende Ringkrane.
Feige. 5.9. Das Absperrventil einer Serie 19041 der Firma FAS (Deutschland). Eigenschaften: Du - 15-200 mm (DIN 2635), ru - bis 4 MPa, Betriebstemperaturbereich - -40 ... + 70 ° С. Gehäusematerial - GS-C25, Stopfen und Spindel - Edelstahl. Das Diagramm zeigt: 1. Gehäuse; 2. Abdeckung; 3. Cork; 4. Spindel; 5. Der Griff; 6. Siegel; 7. Haarnadel; 8. Nuss; 9. Dichtung; 10. Führung; 12. Verschlussstopfen.- Ventile - Absperrventile mit translatorischer Bewegung des Verschlusses in Richtung, die mit der Strömungsrichtung des transportierten Mediums übereinstimmt. Der Verschluss wird durch Einschrauben der Spindel in die Laufmutter bewegt. Grundsätzlich sind die Ventile so ausgelegt, dass sie Strömungen blockieren, aber häufig werden Drosselvorrichtungen mit irgendwelchen Strömungseigenschaften auf ihrer Basis erzeugt.
Im Vergleich zu anderen Ventiltypen haben Ventile die folgenden Vorteile:
die Fähigkeit, bei hohen Druckabfällen auf der Spule und bei hohen Arbeitsdrücken zu arbeiten;
- einfachheit von Design, Wartung und Reparatur;
- der kleine Hub der Spule (im Vergleich zu den Absperrschiebern), der zum Blockieren des Durchgangs erforderlich ist (normalerweise nicht mehr als 1 / 4Dy)
- kleine Gesamtabmessungen und Gewicht;
- dichtheit des Durchgangsverschlusses;
- die Möglichkeit der Verwendung als Regulierungsbehörde und Installation in der Pipeline in jeder Position (vertikal / horizontal);
- sicherheit bezüglich des Auftretens von Wasserschlägen.
Um den Durchfluss in Rohrleitungen mit einer kleinen Nennbohrung und hohen Druckabfällen abzusperren, sind Ventile der einzig akzeptable Typ von Absperrventilen. Der Vorteil von Ventilen gegenüber Absperrschiebern besteht auch darin, dass in ihnen die Spulendichtung leicht aus Gummi oder Kunststoff hergestellt werden kann, während die Dichtkraft erheblich verringert und die Korrosionsbeständigkeit der Dichtung erhöht wird. Häufige Nachteile des Ventils sind:
- hoher hydraulischer Widerstand;
- die Unmöglichkeit ihrer Verwendung in Strömen stark kontaminierter Medien;
- große Konstruktionslänge (im Vergleich zu Absperrschieber und Absperrklappe);
- mittlerer Durchfluss in nur einer Richtung, die durch die Ventilkonstruktion angegeben wird;
- relativ hohe Kosten.
Es gibt jedoch keine Alternativen zu Ventilen zur Steuerung von Strömungen mit hohen Arbeitsdrücken sowie niedrigen oder hohen Temperaturen des Arbeitsmediums.
Die Klassifizierung zahlreicher Ventilkonstruktionen kann nach mehreren Kriterien erfolgen:
- von Natur aus - Durchgangs-, Winkel-, Durchgangs- und Mischventile;
- nach Vereinbarung - Sperren, Sperren und behördliche Vorschriften;
- über das Design von Drosselvorrichtungen - mit profilierten Spulen und Nadel;
- über das Design der Rollläden - Scheibe und Membran;
- nach der Methode der Abdichtung der Spindel - Stopfbuchse und Balg.
Die Eigenschaften der in Gasversorgungssystemen verwendeten Ventile sind in der Tabelle angegeben. 5.15.
Auswahl der Armaturen. Bei der Planung und dem Bau von Gasversorgungssystemen sowie bei der Gasausrüstung von Einheiten und Apparaten in Industrie- und Kommunalunternehmen wird die Auswahl der Armaturen von der Entwurfsorganisation unter Berücksichtigung der physikochemischen Eigenschaften, des Drucks und der Temperatur der Arbeitsumgebung und der Umgebungsluft sowie der Anforderungen der aktuellen technischen Regulierungsdokumente festgelegt.
Das Design und die Materialien der verwendeten Armaturen müssen einen zuverlässigen und sicheren Betrieb der Systeme bei festgelegten Parametern gewährleisten, wobei die Explosions- und Brandgefahr brennbarer Gase zu berücksichtigen ist. Elektrische Ausrüstung von Antrieben und anderen Elementen rohrverbindungsstücke muss die Exerfüllen, die in den Regeln für elektrische Installationen (PUE) angegeben sind.
Die Hauptanforderungen für Absperrventile, die an Gasleitungen installiert sind:
- festigkeit und Dichtheit, unabhängig von der Richtung der Gasbewegung, erfüllen die Anforderungen von GOST 9544-2005;
- korrosionsbeständigkeit;
- explosionsschutz;
- zuverlässiger Betrieb und einfache Wartung;
- schnelles Schließen und Öffnen;
- minimaler hydraulischer Widerstand gegen Gasdurchgang;
- die Fähigkeit, den Gasdurchgang zu kontrollieren;
- kurze Baulänge;
- geringes Gewicht und Gesamtabmessungen.
Die Festigkeit der Bewehrung wird hauptsächlich durch den Arbeitsdruck und die Temperatur bestimmt, die in einem weiten Bereich beliebige Werte haben können. Bei der Auswahl von Armaturen für Gasleitungen sollten die folgenden Eigenschaften von Metallen berücksichtigt werden:
- Gase haben nur geringe oder keine Auswirkungen auf Eisenmetalle, daher können die Armaturen aus Stahl und Gusseisen bestehen. Es ist zu beachten, dass Gusseisenbeschläge aufgrund unzureichend hoher mechanischer Eigenschaften bei Drücken von nicht mehr als 1,6 MPa verwendet werden können. Bei der Verwendung von Gusseisenbeschlägen ist es wichtig, Bedingungen auszuschließen, unter denen die Flansche beim Biegen funktionieren würden.
- Technische Normen beschränken die Verwendung von Gusseisenbeschlägen in explosionsgefährdeten Bereichen.
- Gase, die erhebliche Mengen Schwefelwasserstoff enthalten (mehr als 2 g pro 100 m 3 ) wirken sich sehr aktiv auf Bronze und andere Kupferlegierungen aus, daher wird die Verwendung von Armaturen mit bronzenen Dichtflächen (Ringen) nicht empfohlen. Es sollte auch berücksichtigt werden, wenn die Dichtflächen des Sitzes und des Ventils an den entsprechenden Teilen aus Eisenmetallen (d. H. Ohne Einsatzringe aus) bearbeitet werden aus Edelstahl und Nichteisenmetalle) unterliegen diese Oberflächen unter Betriebsbedingungen schnellem Verschleiß und Korrosion während der Lagerung;
- Rostfreie Stähle sind gas- und lagerbeständig. Für kritische Armaturen können Einsatzringe aus Edelstahl empfohlen werden.
- Dichtringe aus Babbitt können für brennbare Gase für Ventilarmaturen verwendet werden, die bei niedrigen Temperaturen betrieben werden.
- O-Ringe aus Gummi werden in Ventilarmaturen nur bei Temperaturen bis 50 ° C und Druck bis 1,0 MPa eingesetzt;
Beim Speichern und Transportieren brennbarer Gase ist die minimale Wärmekapazität des Ventils erforderlich, damit beim Einschalten die Abkühlzeit auf die Flüssigkeitstemperatur so gering wie möglich ist. Der Ventilkörper muss einen geringen Metallverbrauch bei ausreichend hoher Festigkeit aufweisen.
Bei der Lagerung, Installation und dem Betrieb von Rohrverbindungsstücken müssen folgende Anforderungen erfüllt sein:
- vor dem Einbau der Armaturen muss die Rohrleitung gründlich gereinigt und geschliffen und zerkleinert werden.
- armaturen, die die Bewegungsrichtung des Mediums angeben (Pfeil auf dem Gehäuse), werden nur entsprechend an der Rohrleitung installiert;
- bei der Montage von Flanschventilen müssen die Flansche und Schraubenlöcher mit den Löchern an den Ventilflanschen übereinstimmen. Ziehen Sie die Schrauben gleichmäßig und mit einem normalen Schraubenschlüssel an.
- der Installationsort der Armaturen muss beleuchtet sein, und die Durchgänge zwischen den Armaturen und den Gebäudestrukturen müssen den Normen zur Gewährleistung einer sicheren Wartung und Inspektion entsprechen.
- beim hydraulischer Test Ventilventile müssen für eine lange Lebensdauer vollständig geöffnet sein.
- es ist verboten, Absperrventile als Regel- oder Drosselventile zu verwenden.
- es ist verboten, beim Schließen und Öffnen von Ventilen zusätzliche Hebel zu verwenden.
- das Außengewinde der Spindeln muss mindestens 1 Mal pro Monat geschmiert werden.
- zur Lagerung von Armaturen in einem Lager in der Verpackung des Herstellers oder in unverpackter Form (mit Steckern erforderlich) auf Gestellen in einem trockenen Raum. Während der Langzeitlagerung muss alle sechs Monate das Schmiermittel auf den behandelten Oberflächen der Produkte gewechselt und der festgestellte Schmutz oder Rost entfernt werden.
- armaturen für den vorgesehenen Zweck gemäß den Anweisungen im technischen Datenblatt verwenden, technische Bedingungen, Standards oder besondere Bedingungen der Bestellung;
- es ist verboten, Arbeiten durchzuführen, um Defekte zu beseitigen und die Drüse bei Vorhandensein von Druck in der Gasleitung zu unterbrechen.
- stopfbuchsenschrauben und Stehbolzen sollten gleichmäßig angezogen werden, um Verzerrungen zu vermeiden.
- wenn in den Dichtungen (zwischen Gehäuse und Deckel) und in den Ventilen tödliche Undichtigkeiten festgestellt werden, müssen die Ventile aus der Gasleitung entfernt, zerlegt und sorgfältig geprüft werden. Defekte an den Dichtflächen müssen durch Einlass oder Läppen beseitigt werden, wenn die Möglichkeit einer solchen Reparatur in der Konstruktion vorgesehen ist;
- armaturen, die für kritische Installationen in Betrieb, Reserve oder Reparatur bestimmt sind, werden aufgezeichnet und in einem speziellen Register aufgezeichnet, in dem die Installationszeit, die Inspektion und Reparatur der Produktion, die Art der Reparatur und der Zustand danach angegeben sind.
- wartungspersonal, das Arbeiten zur Konservierung und De-Konservierung von Ventilen ausführt, muss über eine individuelle Schutzausrüstung verfügen und den Brandschutzanforderungen entsprechen.
Allzweckventile werden vor dem Einbau folgenden Prüfungen unterzogen:
- krane - für die Festigkeit und Dichte des Materials von Teilen mit Wasser oder Luft mit einem Druck von 0,2 MPa; die Dichtheit des Verschlusses, der Stopfbuchse und der Dichtungen - Luftdruck gleich 1,25 Arbeit. Krane, die für einen Arbeitsdruck von mindestens 0,04 MPa ausgelegt sind, sollten mit einem Druck von 0,05 MPa getestet werden.
- absperrschieber - für Festigkeit und Dichte des Materials bei einem Wasserdruck von 0,2 MPa und zusätzlich für eine Dichte bei einem Luftdruck von 0,1 MPa; für Verschlussdichtheit - durch Eingießen von Kerosin, während die Testergebnisse den Anforderungen für Ventile der entsprechenden Dichtheitsklasse entsprechen müssen.
Allzweckventile, die an Mittel- und Hochdruckgasleitungen installiert sind, werden wie folgt getestet:
- krane - für Festigkeit und Dichte des Materials mit einem Wasserdruck von 1,5 der maximalen Arbeitsleistung, jedoch nicht weniger als 0,3 MPa; die Dichtheit der Verschlüsse von Verschluss, Dichtung und Stopfbuchse - bei einem Luftdruck von 1,25 der maximalen Arbeitsleistung;
- ventile und Ventile für die Festigkeit und Dichte des Materials - Wasserdruck gleich 1,5 maximaler Arbeit, jedoch nicht weniger als 0,3 MPa mit einem zusätzlichen Dichtetest mit Luft bei gleichzeitiger Überprüfung der Dichtheit der Stopfbuchsen- und Dichtungsdichtungen; für Verschlussdichtheit - Kerosin einfüllen. Gleichzeitig müssen die Prüfergebnisse den Anforderungen an Ventile der entsprechenden Dichtigkeitsklasse entsprechen.
Ventiltests werden bei konstantem Druck für die Zeit durchgeführt, die für eine gründliche Inspektion erforderlich ist, jedoch nicht weniger als 1 Minute. Ein "Schwitzen" des Metalls sowie der Durchgang des Mediums durch das Metall, Stopfbuchsen und Dichtungen sind nicht gestattet.
Vorrichtungen zum Schutz von Teilen von Gasleitungen und Ventilen vor Beschädigung. Solche Einheiten umfassen Teppiche, Luken, Kupplungen, Dehnungsfugen und Gehäuse. Teppiche schützen Gasleitungsgeräte, die die Erdoberfläche erreichen - Wasserhähne, Stopfen, Rohre von Kondensatsammlern, Wasserdichtungen, Steuerleiter - vor mechanischen Beschädigungen. Traditionell werden Teppiche und Luken aus Gusseisengehäusen und Klappdeckeln hergestellt. In letzter Zeit wurden jedoch zunehmend andere Materialien verwendet. Um ein Absinken zu verhindern, werden Teppiche und Luken auf Betonkissen mit leichter Verstärkung installiert. Sicherheitskupplungen aus zwei geschweißten Kupplungshälften werden installiert, um die Betriebssicherheit von Hoch- und Mitteldruckleitungen mit Unsicherheit zu erhöhen schweißnähte oder ihre Unvollkommenheiten.
Kompensatoren werden verwendet, um Spannungen zu reduzieren, die durch Änderungen der Bodentemperatur an den Flanschen von Gusseisenarmaturen verursacht werden, sowie um die Möglichkeit der Demontage, des Dichtungswechsels und der anschließenden Installation zu ermöglichen. Linsenkompensatoren, die zusammen mit Armaturen an unterirdischen Gasleitungen in Bohrlöchern installiert sind, bestehen aus Stahlblech in Form von getrennten, miteinander verschweißten Halblinsen. Um normale Demontage- und Installationsbedingungen zu gewährleisten und Temperaturspannungen von den Ventilflanschen abzubauen, werden Zwei-Linsen-Kompensatoren verwendet, die aus vier Halblinsen bestehen. Linsenkompensatoren werden unter Berücksichtigung ihrer maximalen Kompensationsfähigkeit und Axialkräfte komprimiert installiert. Die maximale Kompensationsfähigkeit des Kompensators wird als wechselseitige Änderung seiner Länge verstanden. Bei einem Kompensator mit mehreren Linsen wird diese Fähigkeit durch die Summe der Kompensationsfähigkeit der einzelnen Linsen bestimmt.
Gehäuse werden verwendet, um Gasleitungen vor mechanischen Einflüssen zu schützen, die sich über und unter den Strukturen befinden, und um zu verhindern, dass Gas in sie eindringt, wenn die Rohrleitungen reißen oder undicht werden. Die Vorrichtung eines einfachen Gehäuses, das zum Verlegen einer Gasleitung durch Fundamente, Wände von Gebäuden und Bauwerken dient, ist in Abb. 1 dargestellt. 5.11.
Die Gaskontrollstellen (HF) von Industrie- und Kommunalunternehmen werden in einem separaten Gebäude errichtet und dienen der Versorgung mehrerer großer Verbraucher (Werkstätten, Kesselhäuser) mit Gas. Frakturen mit einem Eingangsdruck von nicht mehr als 0,6 MPa können in Nebengebäuden von Industriegebäuden mit einem Feuerwiderstandsgrad I und II angebracht werden, wobei Industrien, die als brandgefährlich für die Kategorien G und D eingestuft sind, direkt an Gassteuereinheiten (GRU) und Steuer- und Regelungspunkten (KRP) angebracht sind in den Räumlichkeiten von Werkstätten und Kesselräumen, in denen sich Einheiten befinden, die Gas verwenden.
Die Zusammensetzung des hydraulischen Bruchs (GRU, PKK) umfasst:
- filterreiniger;
- druck-Regler;
- sicherheits-, Verriegelungs- und Entleerungsvorrichtungen;
- absperrventile;
- Instrumentierung;
- gasdurchflussmessgerät (Messgerät oder Messblende).
Das Anfangsdruckgas durch das Ventil tritt in den Filter ein, wo es von mechanischen Verunreinigungen gereinigt wird. Das gereinigte Gas wird durch ein Sicherheitsabsperrventil geleitet, das die Gaszufuhr im Falle einer Notabweichung (maximal und minimal) des Ausgangsdrucks abschaltet. Dann tritt das Gas in den Druckregler ein, den Hauptknoten eines Gassteuergeräts. Es reduziert den Gasdruck auf einen vorgegebenen und hält ihn unabhängig von der Änderung des Gasflusses automatisch aufrecht. Der Druckregler und das Sicherheitsabsperrventil sind über ein Impulsleitungssystem mit der Auslassgasleitung verbunden.
Die Hydraulic Fracturing Control Line verfügt über eine Bypass-Gasleitung (Bypass). Wenn ein Steuerleitungsgerät ausfällt oder während Wartungs- und Reparaturarbeiten, werden die Ventile vor dem Filter und nach dem Schließen des Reglers, dh der hydraulische Bruch, auf die Bypassleitung übertragen, an der zwei Absperrventile installiert sind: Das erste arbeitet im Drosselmodus und übernimmt die Hauptleitung Differenzdruck und der zweite - im Ventilmodus, wobei ein vorbestimmter Ausgangsdruck konstant gehalten wird.
Die Sist so ausgelegt, dass sie den Gasaustrittsdruck nach dem Regler verringert, indem ein Teil des Gases in die Atmosphäre entlüftet wird. Es muss auf einen Druck eingestellt werden, der unter dem maximalen Abschaltdruck des Absperrventils liegt. Bei einem starken Abfall des Gasflusses (der beispielsweise durch das Abschalten eines Teils der gasverbrauchenden Einheiten verursacht wird) der eingestellte Druck und der Gasdruck im Gasversorgungssystem nach einem kurzen Anstieg des Reglers nicht sofort wieder hergestellt. Überdruckventil und entfernt es.
Im Notfallmodus kann das Überdruckventil den Ausgangsdruck aufgrund der geringen Durchflussmenge nicht reduzieren. Der Gasdruck nach dem Regler steigt an, bis er den Abschaltdruck des Sicherheitsabsperrventils erreicht, wodurch die Gaszufuhr zum hydraulischen Aufbrechen unterbrochen wird.
Hydraulic Fracturing ist für den automatischen Betrieb ausgelegt. Zur regelmäßigen Überwachung des Betriebs von Instrumenten und Geräten werden Manometer und zur Messung Durchflussmesser installiert.
In der Praxis werden verschiedene Arten des hydraulischen Brechens verwendet: ein- und zweistufig (zwei Regler sind in Reihe installiert); einfach, doppelt und dreifach (drei Steuerleitungen sind parallel installiert). Eine zweistufige Gasdruckreduzierung dient der Sicherheit und Geräuschreduzierung.
Die parallele Installation von Steuerleitungen ist gerechtfertigt, wenn die Kapazität des Druckreglers nicht den erforderlichen Gasdurchsatz liefert oder wenn sich der Gasdurchsatz im Unternehmen innerhalb eines Bereichs, der größer ist als die zulässigen Änderungen der Kapazität des Reglers, stark ändert. Im Parallelbetrieb von zwei oder mehr Steuerleitungen für das hydraulische Brechen wird jede auf einen Ausgangsdruck eingestellt, der sich geringfügig vom Druck auf der benachbarten Leitung unterscheidet. In diesem Fall werden die Leitungen je nach Last automatisch ein- und ausgeschaltet.
Zur Berechnung und Auswahl des Druckreglers sowie zur Bestimmung der Einstellungen der Ausrüstung werden die Hydraulikleitungen vor und nach der Bestimmung des hydraulischen Bruchs und der Druckverluste berechnet, und die Einstellungen werden gemäß den berechneten Parametern berechnet und während des Betriebs angegeben.
Der minimale Gasabsperrdruck wird unter Berücksichtigung der Druckverluste in den Gasleitungen vom minimalen Gasdruck vor den Brennern abgeleitet. Die vorgeschlagenen Einstellmodi können abhängig vom Gasdruck und der Art der Gasbrenner eingestellt werden.
Steuer- und Verteilungspunkte (PKK) in Form einer kompakten Einheit werden häufig in autonomen Gasversorgungssystemen mit niedrigem und mittlerem Kraftstoffverbrauch eingesetzt.
Das Design des Steuerventils der Firma FAS (Deutschland) umfasst einen Druckregler und einen Gaszähler. Der Steuerungs- und Verteilungspunkt ist vollständig in einem Stahlschrank montiert. Der Anschluss an das KRP erfolgt an der Unterseite des Gehäuses über Kupplungen mit konischen oder zylindrischen Rohrgewinden.
Das Design bietet mehrstufigen Schutz in Notsituationen:
- Bei einem Stromausfall schließt das elektromagnetische Ventil und stoppt die Gasversorgung.
- Bei einem Rohrbruch wird die Gasleitung mit einem Hochgeschwindigkeitsventil abgesperrt;
- Bei einem Gasleck in dem Raum, in dem sich die Gasregeleinrichtung befindet, schließt das elektromagnetische Ventil und unterbricht so die Gaszufuhr.
Das Lieferkit des Bedienfelds enthält:
- Stahlschrank;
- Gaszähler;
- Druckregler (Abb. 5.13);
- Kupplungen;
- Kugelhähne;
- Druckanzeige;
- Hochgeschwindigkeits-Absperrventil;
- T-Verbindungen;
- Magnetventil.
Geräuschreduzierung beim hydraulischen Brechen / Brechen. Bei hohen Kosten und Druckabfällen in den Reglern können Geräusche und Vibrationen auftreten, deren Intensität durch die technologische Funktionsweise der Geräte, die Konstruktion der Steuergeräte und die akustischen Eigenschaften des hydraulischen Bruchgebäudes bestimmt wird. Das Geräusch des hydraulischen Bruchgebäudes breitet sich hauptsächlich durch Türen, Fenster, das Lüftungssystem (Abweiser, Rollläden usw.) und andere Öffnungen aus. Die Hauptlärmquellen sind:
- druckregelventilvorrichtung;
- leitungselemente hinter dem Regler;
- linsenkompensatoren, steile Biegungen, Gewindebohrer, Verschlussventile usw.;
- ausgehende Gasleitungen.
- reduzieren Sie das Rauschen in der Quelle selbst, indem Sie die Frequenz und die Welligkeitszonen reduzieren.
- lokalisieren Sie Geräusche aufgrund der Schalldämmung der Geräuschquelle.
- erhöhen Sie die Schalldichte des Bruchgebäudes.
Für das vorhandene hydraulische Brechen ist es ratsam, einen passiven Schutz zu verwenden, der auf der Verwendung von schallabsorbierenden Materialien und Strukturen basiert, um die "lautesten" Knoten der Steuerleitung schalldicht zu machen und die akustische Dichte der hydraulischen Brechanlage selbst zu erhöhen. Die folgenden Methoden gehören zu dieser Art von Schutz:
- aufbringen schallabsorbierender Beschichtungen auf die Außenfläche
- gasleitungen und Armaturen;
- installation eines schalldichten Gehäuses;
- auskleidung mit schallabsorbierendem Material der Innenflächen des Diffusors, der Haube der Abgasabweiser und der Öffnungen der Lamellengitter (in diesem Fall ist es notwendig, den normativen Luftaustausch der Belüftung aufrechtzuerhalten);
- erhöhung der Schalldichte von Fenstern und Türen (Doppeltüren mit schallabsorbierendem Material beschichtet, Doppel- oder Dreifachfenster mit schallabsorbierendem Material entlang des Umfangs der Öffnungen).
Schaumgummi (Polyurethanschaum), Mineralwollplatten mit hohen Nachhaim Hochfrequenzband des Geräuschspektrums (0,75–0,98) können als schallabsorbierende Materialien in Strukturen verwendet werden. Als schallabsorbierende Beschichtungen für Gasleitungen werden spezielle Bitumen-Gummi-Kitte verwendet.
Merkmale der Gasversorgung von Produktionsstätten (Werkstätten, Werkstätten usw.). Die Produktionsstätten werden mit Gas mit niedrigem oder mittlerem Druck versorgt, das von der Art und Menge der Wärmeerzeugungseinheiten sowie den Anforderungen der "Sicherheitsregeln im Gasmanagement" und des SNiP 42-01-2002 "Gasverteilungssysteme" bestimmt wird. Die allgemeinen Elemente des Werkstattgasleitungsschemas lauten wie folgt:
- eine allgemeine Trennvorrichtung am Einlass der Gasleitung zur Werkstatt, unabhängig vom Vorhandensein einer Trennvorrichtung an der Gasleitung zwischen den Werkstätten vor der Werkstatt;
- zeigen eines Manometers am Gasleitungseinlass zur Werkstatt nach einer allgemeinen Trennvorrichtung;
- gasdurchflussmessgerät;
- trennen von Vorrichtungen an Abzweigungen von Gasleitungen zu Einheiten;
- spülen Sie Gaspipelines, die die Entfernung von Luft und Gas-Luft-Gemisch während des Startvorgangs aus allen Gaspipelines innerhalb des Geschäfts sicherstellen.
Das Gasversorgungsschema der Werkstatt (Heizraum) in Abb. 5.14, kann für Gasversorgungssysteme mit niedrigem und mittlerem Gasdruck verwendet werden, jedoch nach hydraulischem Brechen. Wenn das Gasversorgungssystem des Unternehmens die Installation in der GRU / KRP-Werkstatt vorsieht, wird es im Gasversorgungskreis der Werkstatt zwischen der gemeinsamen Trennvorrichtung und dem Gasdurchflussmesspunkt montiert.
Die in die Werkstatt eintretende Gasleitung wird in der Regel in einem Fall durch die Gebäudewand geführt (Abb. 5.11). Der Raum zwischen dem Gehäuse und der Gasleitung ist mit einem geteerten Leinenstrang bedeckt und an den Enden mit Bitumen gefüllt. Das Gehäuse soll die Rohrleitung vor Beschädigungen bei geringfügigen saisonalen oder anderen Wandverformungen schützen. Direkt am Einlass der Gasleitung wird eine allgemeine Trennvorrichtung (Ventil, Ventil) an einem zugänglichen und beleuchteten Ort zur Wartung installiert. Gasleitungen in Werkstätten werden offen an Wänden, Säulen und anderen Strukturen an Stellen verlegt, die für die Wartung geeignet sind und die Möglichkeit einer Beschädigung durch Werkstatttransport ausschließen. Es ist nicht gestattet, Gasleitungen durch Keller, Räume der Explosionsindustrie, Lagerhäuser für explosive und brennbare Materialien, Räume für elektrische Verteilungsgeräte und Umspannwerke, Lüftungskammern sowie durch Räume zu verlegen, in denen die Rohrleitung korrosionsanfällig ist (Gießen, Schlacke, Vorbereitung usw.). Gasleitungen sollten auch nicht im Bereich direkter Wärmestrahlung aus den Öfen verlegt werden, an Orten, an denen sie mit heißen Verbrennungsprodukten oder Kontakt mit heißem oder geschmolzenem Metall gewaschen werden können.
Gasleitungen werden mit speziellen Metallklammern oder Anhängern mit Klemmen befestigt. Wenn sich die Ventile in einer Höhe von mehr als 2 m befinden, werden Aussichtsplattformen mit Treppen angeordnet oder ein Fernantrieb bereitgestellt. Wenn die Armaturen gelegentlich verwendet werden, kann das Wartungspersonal die Leitern benutzen. Die Abstände zwischen den Gasleitungen und den Wänden der Werkstatt werden auf der Grundlage einer einfachen Inspektion und Reparatur von Gasleitungen, Flanschverbindungen, Armaturen und Geräten ausgewählt. An den Durchgangsstellen von Personen sollten Gasleitungen in einer Höhe von mindestens 2,2 m verlegt werden, vom Boden bis zum Boden der Leitung.
In Werkstätten und Kesselräumen werden in der Regel Gasleitungen oberirdisch verlegt. Wenn sich die Wärmeerzeugungseinheiten an Orten befinden, an denen keine oberirdischen Gasleitungen verlegt werden können, dürfen sie ausnahmsweise unterirdisch in Betonkanälen mit oberen abnehmbaren Platten verlegt werden. Die Abmessungen der Kanäle werden basierend auf der Möglichkeit der Installation und der Benutzerfreundlichkeit ausgewählt. Der freie Raum zwischen dem Kanal und der Gasleitung ist mit Sand bedeckt, um die Möglichkeit einer Gasansammlung auszuschließen. Bei dauerhafter Belüftung kann der Kanal mit der Gasleitung nicht mit Sand gefüllt werden. Gasleitungen in den Kanälen sollten eine Mindestanzahl von Schweißverbindungen aufweisen. Gewinde, Flanschverbindungen sowie der Einbau von Ventilen in die Kanäle sind verboten.
Feige. 5.16. Gaspipeline-Eingabeeinheit.Die Gaspipelines an den letzten entfernten Standorten sind mit Spülgaspipelines ausgestattet, mit denen Gaspipelines aus der Luft freigesetzt werden können, bevor die Wärmeerzeugungseinheiten gestartet und das Gas während der Reparatur, Konservierung oder langfristigen Abschaltung des Gasversorgungssystems durch Luft verdrängt werden. Spülgasleitungen von Einheiten (Öfen, Kessel, Trockner usw.) können auch an Werkstatt-Spülgasleitungen angeschlossen werden. Abblaseleitungen werden aus Gebäuden herausgeführt und an der Außenfläche der Wände mindestens 1 m über der Dachvorsprung an einem Ort verlegt, an dem das Gas sicher verteilt wird. Um die Möglichkeit von Regen auszuschließen, wird das Ende der Gasleitung entweder gebogen oder ein Schutzschirm darauf montiert.
Rohre werden durch Gasschweißen verbunden. Gewinde- und Flanschverbindungen sind an den Installationsorten von Armaturen, GRU-Geräten, Instrumenten und Gasbrennern zulässig.
Gaspipelines. Die Wahl des Rohrleitungsschemas für thermische Einheiten (Kessel, Industrieöfen, Trockner usw.) hängt von der Wärmekapazität der Einheit, der Art und Anzahl der Brenner, dem Gasdruck im System, der Art der Trennvorrichtungen (Hähne oder Ventile) sowie der Art des verwendeten Automatisierungssystems ab Regulierung und Sicherheit. Über viele Jahre hat sich gezeigt, dass Hähne und Ventile durch die Zuverlässigkeit des Abschaltens (Dichtheit) effizienter sind als Absperrschieber. Selbst ein kleines Gasleck wird sofort durch Geruch erkannt, da Gas, das durch eine Öldichtung oder einen Stopfen strömt, normalerweise in den Raum und nicht in den Ofen gelangt. Die unzureichende Dichte des Ventils führt zu erheblichen Gaslecks in den Ofen, und es ist fast unmöglich, diese Lecks ohne spezielle Vorrichtungen zu erkennen.
Die Varianten der Rohrleitungsrohre sind sehr unterschiedlich und hängen stark von den Gerätetypen, ihrer Konstruktion und den verwendeten internen Geräten (Gasbrenner, Automatisierungseinheiten, Trenn- und Dosiergeräte) ab. Daher sollten in jeder Situation eigene Systeme entwickelt werden, die an die örtlichen Gegebenheiten angepasst sind.
Sicherheits-Explosionsventile. Der größte Druck während der Explosion eines Gas-Luft-Gemisches in begrenzten Volumina erreicht 1 MPa (10 atm) (Tabelle 5.18). Die meisten Elemente der Gebäudehülle kollabieren bei einem Druck von bis zu 0,05 MPa: Ziegelwände mit einer Dicke von 51 cm kollabieren bei einem Druck von 0,050 MPa, 38 cm dick - 0,020 MPa und verglaste Fensteröffnungen - bei nur 0,002 MPa. Eine Explosion eines Gas-Luft-Gemisches in Öfen und Abzügen führt zu einer sofortigen adiabatischen Ausdehnung der Verbrennungsprodukte und einem Druckanstieg, der die Gebäudehülle einer thermischen Anlage zerstören kann. Die Bildung explosiver Gas-Luft-Gemische kann auftreten, wenn Gas durch das Ventil austritt, die Brennerflamme während des Betriebs erlischt usw. Selbst kleine Gaslecks sind gefährlich, da die Volumina der Öfen und Gaskanäle relativ klein sind.
Um die Zerstörung der umschließenden Strukturen der Öfen und Abzüge von thermischen Anlagen zu verhindern, werden Sicherheitssprengventile installiert, die bei Drücken arbeiten, die niedriger sind als die zerstörerischen Strukturen von Druckanlagen. Diese Ventile sorgen für eine rechtzeitige Druckentlastung der Verbrennungsprodukte aus der Kammer, in der die Explosion auftritt.
Am weitesten verbreitet sind Ventile mit Berst-, Falt- und Entlastungsarten, die an den Decken und Wänden von Öfen und Gaskanälen installiert sind. Ventile werden in Bereichen installiert, in denen sich am wahrscheinlichsten Gaslecks ansammeln und sich Gassäcke bilden. Sie müssen so positioniert werden, dass das Servicepersonal beim Abfeuern durch eine Druckwelle nicht betroffen ist. Wenn dies nicht möglich ist, muss nach dem Ventil eine Schutzbox oder ein Visier angebracht werden, die fest mit dem Gerät verbunden sind und den explosiven Auspuff zur Seite leiten. Die Form der Strahlventile sollte quadratisch oder rund sein, da in diesem Fall weniger Druck erforderlich ist, um die Membran aufzubrechen.
Das Berstventil hat eine Membran aus Asbestblech mit einer Dicke von 2-3 mm, die durch eine Explosion zerstört wird. Durch das geformte Loch werden die Verbrennungsprodukte in die Umgebung abgegeben. Um die Festigkeit und Haltbarkeit vor der Membran zu erhöhen, ist an der Seite des Ofens ein Metallgitter mit Zellen von 40 x 40 oder 50 x 50 mm angebracht. Asbestplatte und -gitter werden mit Flanschen festgeklemmt, an denen sie befestigt sind metall-Boxfest in der Auskleidung der Thermoeinheit montiert. Es ist zu beachten, dass die Asbestplatte bei Temperaturen bis zu 500 ° C lange arbeiten kann. Daher sind die Sprengventile so installiert, dass die Asbestmembran nicht der Hitze des Brenners und des Glühlampenmauerwerks ausgesetzt ist. Explosive Ventile sind einfach und kostengünstig.
Bei Klappventilen öffnet sich bei einer Explosion im Ofen das Ventil und gibt eine Öffnung für die Emission von Verbrennungsprodukten frei. Um eine Überhitzung zu vermeiden, ist das Ventil an der Seite des Ofens mit einer Lösung aus feuerfestem Ton mit Asbest entlang eines verstärkenden Metallgitters ausgekleidet. Im geschlossenen Zustand ist das Klappenventil mit feuerfestem Kitt um den Umfang herum abgedichtet.
Überdruckventile sind eine horizontal verlegte Platte, die im Falle einer Explosion entsorgt wird. Je nach Installationsort und Temperaturbedingungen kann die Entladungsplatte entweder aus einer Asbestplatte mit einer Dicke von 8 bis 10 mm hergestellt, auf ein Metallgitter gelegt und mit feuerfestem Ton um den Umfang herum versiegelt werden, oder aus einer Mischung aus feuerfestem Ton mit Asbestspänen. Diese Platte ist mit einem Metallgitter verstärkt und kann bei Temperaturen bis zu 500 ° C verwendet werden.
Die Berechnung und Auswahl von Sicherheits-Explosionsventilen erfolgt gemäß den geltenden SNiP 42-01-2002, „Sicherheitsregeln in der Gasindustrie“ und „Regeln für Auslegung und sichere Operation Dampf- und Heißwasserkessel. " Im Allgemeinen wird empfohlen, sich auf die folgenden Parameter zu konzentrieren:
- auf 1 m 3 Das Innenvolumen des Ofens, der Gaskanäle und der Schweine sollte mindestens 0,025 m betragen 2 explosives Ventil, während die minimale Ventiloberfläche 0,15 m beträgt 2 ;
- Über dem Ofen müssen Sprengventile mit einer Gesamtfläche von mindestens 0,2 m für leistungsstarke Geräte installiert werden 2 und an Gaskanälen - mindestens zwei Ventile mit einer minimalen Gesamtoberfläche von 0,4 m 2 .
Um Unternehmen und die Bevölkerung mit Erdgas zu versorgen, werden verzweigte Gasversorgungsnetze entwickelt und implementiert, die aus Gasverteilungspunkten, Absperr-, Mess- und Regelventilen und Rohrleitungen mit unterschiedlichem Druck bestehen. Bei Rohrleitungen werden verschiedene Rohrleitungen für Gasleitungen verwendet.
Die Verwendung von Stahlgasleitungen
Gasmetallrohre sind Stahl (GOST 3262-75) und Kupfer (GOST R 52318-2005). Kupferrohre mit kleinem Durchmesser werden in Pipelines von Haushaltsgasnutzungsgeräten verwendet, und Stahlrohre für Gaspipelines werden verwendet, wenn Pipelines mit unterschiedlichem Druck von Hauptpipelines zu Gasrohren für industrielle und häusliche Gasverbrauchsanlagen verlegt werden.
Stahlgasrohre mit Korrosionsschutzbeschichtung
Erdgastransportleitungen werden je nach Maximaldruck in folgende Klassen eingeteilt:
- hochdruck (Kategorien I und II - bis zu 12 bzw. 6 atm);
- mittlerer Druck (bis zu 3 atm);
- niedriger Druck (bis zu 0,05 atm).
Je nach Arbeitsdruck, Außendurchmesser und Verlegemethode (außen oder innen, oberirdisch oder unterirdisch) stellen Rohre unterschiedliche Anforderungen an Stahlsorte, Wandstärke und Korrosionsschutzbeschichtung.
Rohre für Gasleitungen werden gemäß GOST 31447-2012 geschweißt. Die Wandstärke wird in Abhängigkeit vom Sicherheitsniveau der Route gemäß SNiP 2.05.06-85 berechnet. Autobahnen bestehen aus Rohren für eine Hochdruckgasleitung. Mitteldruckleitungen werden zur Versorgung von Wohngebäuden und Industrieanlagen verlegt und sind niedrig - bei der Gasversorgung für die Verbrennung in Brennern.
Es gibt folgende Arten von Korrosionsschutzbeschichtungen:
- verzinken;
- zwei- oder dreischichtiges Polyethylen;
- korrosionsschutzfarbe zur Wärmedämmung.
Der Schutzgrad wird durch den Standort der Route und den Grad des Risikos bei Verletzung der Dichtheit der Wände bestimmt.
Gasleitungen aus Kunststoffrohren
Polyethylen-Gasleitungen, die mit einem gelben Streifen elektromagnetischer akustischer Diagnostik gekennzeichnet sind
Zur Versorgung kleiner Siedlungen mit Gas gemäß SNiP 42-01-02 und PB 12-529-03 in Hochdruckleitungen der Kategorie II können Polyethylenrohre (HDPE) verwendet werden, die gemäß TU 6-19-051-538-85 hergestellt wurden. Für Rohrleitungen mit mittlerem und niedrigem Druck ist die Verwendung von Rohren des Typs C zulässig. Kunststoffrohre für eine Gasleitung unterliegen Einschränkungen hinsichtlich der Verwendung von:
- nicht anwendbar in Städten und großen Siedlungen;
- gas darf keine chlorierten und aromatischen Kohlenwasserstoffe enthalten;
- nur zulässige externe unterirdische (tiefer als 1 m) Rohrverlegung;
- seismizität der Liegefläche - nicht höher als 6 Punkte;
- lufttemperatur - nicht niedriger als 40 ° С;
- einschränkungen der Bodencharakterisierung.
Zu den Vorteilen von Polyethylen (HDPE) gehören ein geringes spezifisches Gewicht und eine hohe Korrosionsbeständigkeit, die die Montage erheblich erleichtern und bei ordnungsgemäßer Installation den Betrieb von Rohrleitungen über einen langen Zeitraum (bis zu 50 Jahre) ermöglichen.
Die Vorrichtung eines dreischichtigen Polyethylenrohres
Andere kunststoffrohre viel seltener oder gar nicht anwenden. Vinyl-Kunststoff verträgt daher keine negativen Temperaturen (der zulässige Wert beträgt minus 5 ° C) und verformt sich unter Last, und Polypropylen für eine Gasleitung wird aufgrund der hohen Gasdurchlässigkeit überhaupt nicht verwendet.
Entwurf und Bau von Gaspipelines
Kontaktloser Ultraschallscanner
Die Planung und der Bau von Gasleitungen aus Metall- und Polyethylenrohren erfolgt gemäß SNiP 2.04.08-87 und SNiP 42-01-2002. Diese Normen legen die Gasroutendiagramme für den Gastransport unter verschiedenen Bedingungen und Empfehlungen für die Auswahl von Rohren und Korrosionsschutzbeschichtungen fest. Der Bau von Pipelines erfolgt streng nach dem entwickelten Projekt und unter Umsetzung der Anforderungen von SNiPs, Sicherheitsregeln sowie unter Aufsicht des General Designers.
Entwurf der Gasleitung, Verlegungsschema
Um Unfälle und technologische Katastrophen zu vermeiden, müssen Gaspipelines regelmäßig überprüft werden. Zur Prüfung des Zustands von Oberflächen werden zerstörungsfreie Prüfmethoden und -geräte für die Außen- und Innenrohranwendung verwendet. Wirbelstrom- und Ultraschall-Fehlerdetektoren sind zur äußerlichen Anwendung bestimmt.
Die Inline-Diagnose von Gasleitungen wird gemäß GOST R 55999-2014 durchgeführt. Der am weitesten verbreitete magnetische Fehlerdetektor, der nicht nur Diagnosen durchführt, sondern auch Ablagerungen von der Innenseite der Rohrwand entfernt. Wenn ein Defekt festgestellt wird, wird der Zugang zum beschädigten Bereich an einer genau definierten Stelle geöffnet, was für die unterirdische Installation wirtschaftlich vorteilhaft ist. Ein Roboterkomplex der elektromagnetisch-akustischen Diagnostik wurde entwickelt und ist bereits in Betrieb. Das Diagnosegerät in den Pipelines bewegt sich auf einer mobilen Fernbedienung.
In-Tube-Magnetfehlerdetektor
Bei der Entwicklung, Installation, dem Betrieb und der Inspektion von Gaspipelines müssen alle gesetzlichen Anforderungen für eine unterbrechungsfreie und störungsfreie Gasversorgung der Verbraucher strikt eingehalten werden.
Video: Herstellung von Stahlrohren für Gaspipelines im metallurgischen Werk Vyksa
Die Gasleitung ist für den Transport eines brennbaren Gemisches ausgelegt, das zur Kategorie der gefährlichen Stoffe gehört. Diese Umstände erfordern spezielle Materialien und Netzwerkbedingungen, die Leckagen ausschließen. Stahlrohre für Gaspipelines wurden vom Beginn der weit verbreiteten Vergasung bis heute verwendet. Und obwohl ihre Kunststoffgegenstücke auf dem modernen Markt erschienen, konnten sie traditionelle Produkte nicht ersetzen, obwohl sie eine Reihe von Vorteilen haben.
Was sind Stahlrohre und Gasleitungen?
Für Gasversorgungsnetze stehen verschiedene Rohrtypen zur Verfügung. Sie können in zwei Hauptgruppen unterteilt werden:- nahtlos
- geschweißt.
Die erste Gruppe besteht aus heiß und kalt verformt, und die Produkte der zweiten Gruppe unterscheiden sich in der Art der Naht - gerade oder spiralförmig. Bei der Herstellung von Rohren werden verschiedene Kohlenstoffstahlsorten verwendet, die in GOST 380-2005 spezifiziert sind. Die Verwendung der einen oder anderen chemischen Zusammensetzung von Stahl, die Art und Größe der Gasleitungen hängt von mehreren Faktoren ab:
- systemdruck - hoch, mittel, niedrig;
- pipeline-Standorte - oberirdisch, unterirdisch, unter Wasser, in einem Gebäude;
- netzwerkziel - Backbone, Verteilung, Backup.
Gaspipelines werden in zwei Kategorien unterteilt. Sie transportieren explosive Gemische unter Druck von bis zu 10 MPa über beträchtliche Entfernungen. In diesem Fall werden Stahlrohre mit großen Durchmessern verwendet, an die höchste Anforderungen gestellt werden.
Verteilungsnetze liefern Gas direkt an die Analysepunkte, dh an den Verbraucher. Solche Rohrleitungen haben einen kleineren Durchmesser und dünnere Wände. Es gibt verschiedene Nuancen. Beispielsweise kann eine Gasleitung in Wohnungen verlegt werden - Stahl oder Kunststoff in Form eines flexiblen Schlauchs.
In Bezug auf das Backup-Netzwerk können wir sagen, dass es für spezielle Zwecke bestimmt ist - strategisch. Es werden erhöhte Anforderungen an es gestellt, da es in bestimmten Situationen möglicherweise nicht verwendet wird.
Gasleitungen müssen über ein Zertifikat und Begleitdokumente verfügen, aus denen der Hersteller und Informationen zu den durchgeführten Prüfungen, der Herstellungsmethode und der Stahlsorte, einem Konformitätszeichen und der GOST-Nummer hervorgehen.
Sortierstandards
GOST 3262-75
Diese Norm bezieht sich auf die Herstellung von Gas- und Wasserleitungen für die Installation von Verteilungssystemen, die Erdgas unter hohem Druck (bis zu 1,6 MPa) liefern. Der Nenndurchmesser der Produkte beträgt bis zu 150 mm Länge - von 4 bis 12 Metern.
GOST 8734-75
Das normative Dokument gibt die Auswahl an nahtlosen Rohren an, die durch Kaltumformen hergestellt wurden. Sie halten einem Druck von bis zu 10 MPa stand. Die maximale Größe des Außendurchmessers beträgt 250 mm. Die gemessene Länge variiert zwischen 4,5 und 9 Metern.
GOST 8732-78
Es bestimmt auch das Sortiment nahtloser Rohre, die jedoch nicht kalt, sondern heiß verformt sind. Ihr Außendurchmesser ist groß - bis zu 530-550 mm bei einer Wandstärke - bis zu 75 mm. Die Produkte werden in einer Länge von 4-12,5 Metern geliefert. Rohre können installiert werden gaspipelines hoher Druck.
GOST 10704-91
Die Norm legt das Sortiment an elektrisch geschweißten Rohren mit gerader Naht fest. Ihr Außendurchmesser kann 1420 mm erreichen. Die Länge der Produkte hängt von ihrem Durchmesser ab. Es variiert von 2 bis 12 Metern.
Vor- und Nachteile von Stahlgasleitungen
Die positiven Eigenschaften der Produkte umfassen:
- ausreichende Festigkeit;
- leichte lineare Ausdehnung;
- fähigkeit, hohem Druck standzuhalten;
- hundertprozentige Dichtheit bei ordnungsgemäßem Andocken und ohne Mängel.
Negative Seiten:
- die Möglichkeit der Kondensation aufgrund hoher Wärmeleitfähigkeit;
- hohe Wahrscheinlichkeit von Korrosionsprozessen;
- mangelnde Flexibilität;
- mühsame Installation durch Schweißen.
Installationsvoraussetzungen
Das Verlegen von Gaspipelines sorgt für die Einhaltung bestimmter Regeln:
- die Entwurfsposition muss unbedingt eingehalten werden.
- die Verbindungen müssen qualitativ hochwertig ausgeführt werden, um Gaslecks während des Betriebs zu vermeiden.
- die Rohre sollten so montiert werden, dass sie genau auf den Sockel passen.
- die Sicherheit der werksseitigen Korrosionsschutzisolierung ist ein wichtiger technologischer Moment, von dem die Störfestigkeit von Stahlwänden gegen den Einfluss von Streuströmen sowie das Fehlen von Rostprozessen abhängt.
- schweißnähte unterliegen einer obligatorischen Behandlung mit Verbindungen auf Bitumenbasis.
Die Isolierung der zum Verlegen in den Boden bestimmten Gasleitungen erfolgt im Werk. Eine qualitativ hochwertige Umsetzung auf der Baustelle ist aufgrund der technologischen Merkmale des Prozesses nicht möglich. Abhängig von den Bodenverhältnissen kann die Schutzbeschichtung normal und verstärkt sein.
Die Gasversorgung ist eines der wichtigsten Themen, die beim Bau und der Verbesserung eines Privathauses berücksichtigt werden müssen. Diese Aufgabe liegt jedoch nicht nur bei den Eigentümern, sondern auch bei spezialisierten Diensten, da das Verlegen und Anschließen einer Gasleitung ausschließlich für diese Dienste ein Problem darstellt.
Bei alledem ist es notwendig, die Klassifizierung von Gasversorgungssystemen sowie die Klassifizierung der einzelnen Komponenten solcher Systeme zu kennen. Zum Beispiel, welche Art von Gasleitungen kann sein, damit Sie Ihre Wünsche in dieser Angelegenheit richtig ausdrücken können.
Was sind die Gasleitungen
Alle Gasleitungen werden je nach Druck in verschiedene Typen unterteilt. Die folgenden Typen können durch diesen Indikator unterschieden werden:
- Hoher Druck. In ihnen kann es von 0,6 bis 1,2 Megapascal reichen. Diese Systeme fallen in die erste Kategorie;
- Hoher Druck mit Betriebsanzeigen von 0,3 bis 0,6 MPa. Diese Systeme fallen in die zweite Kategorie;
- Mitteldruck mit Betriebsanzeigen von 0,005 bis 0,3 MPa;
- Niederdruck mit Anzeigen von 0 bis 0,005 MPa.
Es muss sofort gesagt werden, dass das Material, aus dem die Gasleitung hergestellt werden soll, nicht nur vom Druck abhängt, sondern auch von vielen anderen Faktoren. Genau genommen ist der Druck im Allgemeinen gering, was davon abhängt, da die moderne Industrie sogar Kunststoffrohre herstellt, die in diesem Parameter mit Metall konkurrieren können.
Im Allgemeinen können Gasleitungen in einem Abschnitt anhand der folgenden Faktoren ausgewählt werden:
- Die Situation des Dorfes;
- Bodeneigenschaften;
- Aggressivität von Streuströmen und vielen anderen.
Was sind die Rohre
Wenn wir nun wissen, was Gasversorgungssysteme sein können, sollten wir ihre einzelnen Komponenten - Rohre - betrachten. Gasleitungen wurden früher nur durch ein Material dargestellt - Stahl. Wie bereits erwähnt, produziert die Industrie heute auch Gasleitungen aus Polyethylen. Gleichzeitig sind sie hinsichtlich ihrer Betriebseigenschaften den Metallmerkmalen nicht viel unterlegen.
Übersicht über Kunststoffprodukte
Gasleitungen auf dem Gelände aus Kunststoff zeichnen sich durch eine hohe Beständigkeit gegen verschiedene atmosphärische Niederschläge aus. Darüber hinaus zeigen sie chemisch auch eine hervorragende Stabilität.
Heimkunststoffprodukte sind ziemlich langlebig. Daher können sie leicht in offenen Bereichen und sogar unter sehr rauen klimatischen Bedingungen eingesetzt werden. Sie können alle ihre positiven Eigenschaften auch bei sehr niedrigen Temperaturen beibehalten - bis zu -60 Grad.
Ein weiterer großer Vorteil von Kunststoff ist, dass er keine Angst vor Streuströmen hat, da Polyethylen selbst kein Leiter ist.
Unter anderem ist zu beachten, dass alle Rohre aus Polyethylen keinen zusätzlichen Schutz benötigen, da sie im Gegensatz zu Stahlprodukten keine Angst vor Feuchtigkeit haben.
Ein weiterer wichtiger Vorteil sind die Kosten. Es unterscheidet sich praktisch nicht von den Kosten für Stahlprodukte.
Wichtig! Bei all diesen positiven Eigenschaften werden im Haus selbst nur Metallrohre empfohlen, aber es kann auch Polyethylen in den Boden eingebracht werden.
Im Allgemeinen gelten folgende Einschränkungen für die Verwendung dieser Produkte:
- Es wird nicht empfohlen, Polyethylen in Bereichen zu verwenden, in denen die Temperatur unter 45 Grad fallen kann.
- Legen Sie Kunststoffprodukte nicht in Bereiche, in denen die seismische Aktivität mehr als 6 Punkte erreichen kann.
- Kunststoff wird auch nicht in der Stadt verwendet, in der die Hauptgasleitung zur ersten oder zweiten Kategorie gehört, dh sie hat einen sehr hohen Druck.
- Solche Produkte werden nicht für die Installation von Rohrleitungen unter der Erde und am Boden sowie innerhalb des Hauses, wie bereits erwähnt, in Tunneln und Sammlern verwendet.
In all diesen Fällen können nur Stahlrohre verwendet werden.
Stahlprodukte
Es sollte sofort gesagt werden, dass alle Stahlwerkstoffe einer elektrochemischen und Korrosionsschutzbehandlung unterzogen werden. Dies wird ihre Lebensdauer erheblich verlängern. Aufgrund dessen steigen die Kosten für die gesamte Struktur im Vergleich zu den Kosten für die Konstruktion von Kunststoffelementen erheblich.
Ich muss sagen, dass solche Materialien eine eigene Klassifizierung haben, da sie seit sehr langer Zeit hergestellt werden. Die Aufteilung in Typen erfolgt zunächst durch das Vorhandensein von Schweißnähten:
- Geschweißt;
- Nahtlos.
Alle diese Materialien können aus einer Mischung aus Weichstahl und Struktur hergestellt werden rostfreier Stahl. Unter anderem gibt es solche Zusatzstoffe:
- Schwefel, ungefähr 0,056%;
- Phosphor, ungefähr 0,25%;
- Kohlenstoff, ungefähr 0,046%.
Der Gast hat festgestellt, dass die Wand eine Mindestdicke von ca. 3 mm haben sollte, wenn es sich um Materialien handelt, die für unterirdische Arbeiten bestimmt sind, und mindestens 2 mm für Materialien, die für Bodenarbeiten oder Arbeiten im Haus bestimmt sind.
Unter diesem Gesichtspunkt lassen sich folgende wichtige Merkmale unterscheiden:
- Wandstärke;
- Nenndurchmesser;
- Der Durchmesser der Gasleitung oder die Summe der ersten beiden Parameter.
So können Stahlrohre wie Kunststoffrohre je nach Widerstandsdruck in drei Kategorien unterteilt werden:
- Zum Verlegen unter Tage mit einem Arbeitsdruck von bis zu 1,2 MPa. In diesem Fall kann die Außentemperatur -30 Grad erreichen;
- Für Arbeiten auf Böden mit einem Arbeitsdruck von bis zu 1,2 MPa. Gleichzeitig sollte die Außentemperatur nicht unter -10 Grad liegen.
- Zur Installation im Haus mit einem Arbeitsdruck von bis zu 0,3 MPa. Darüber hinaus überschreitet der Außendurchmesser solcher Produkte 15,9 cm nicht. Die Wandstärke beträgt etwa 5 mm. Die Temperatur des Produkts während des Betriebs sollte nicht unter 0 Grad liegen.
Es ist zu beachten, dass alle Gasleitungen einer Korrosionsschutzbehandlung unterzogen werden müssen. In den meisten Fällen besteht diese Behandlung in der Färbung in einer charakteristischen hellgelben Farbe.