Газопроводи споруджують для транспортування до споживачів природного газу. Проектують їх проектні організації, які отримали ліцензію на проведення подібних робіт. Для монтажу газопроводів застосовуються труби з різних марок сталі різними способами (При різній температурі і тиску) .По методу виробництва сталеві труби для газу можна розділити на безшовні (гарячодеформовані і холоднодеформовані) і зварні (з прямим і спіральним швом).
Сталь для виробництва виробів цього виду повинна відповідати ГОСТ-у 380 88. Технічні характеристики регламентує ГОСТ 1050 88. Товщину труб визначають за допомогою розрахунків, враховуючи, що для підземного трубопроводу вона повинна бути не менше 3-х мм, для наземних - не менше 2-х мм. Газова труба обов'язково повинна мати сертифікат. У документах повинен бути зазначений виробник, ГОСТ, марка стали, метод виробництва, відомості про випробування, номер партії, відмітка ОТК про відповідність.
Сфери застосування сталевих труб для газопроводів:
- - в системах газопостачання з тиск до 1,6 МПа - водогазопровідні труби (ГОСТ 3262-75) з умовним проходом до 80 мм;
- - в газопроводах з різним тиском - безшовні сталеві труби (ГОСТ 8734-75 і ГОСТ 8732-78), що витримують тиск до 10 МПа;
- - в газопроводах з високим тиском - зварні прямошовні труби (ГОСТ 10704-76) з діаметром від 30 до 426 мм і товщиною стінки від 3-х до 12-и мм.
Переваги сталевих труб для газу
Сталеві труби для газопроводів:
- - міцні;
- - стійкі до внутрішнього тиску;
- - лінійне розширення сталевих труб в 20 разів менше, ніж у труб з поліетилену;
- - стовідсоткова газова герметичність, що виключає протікання газу.
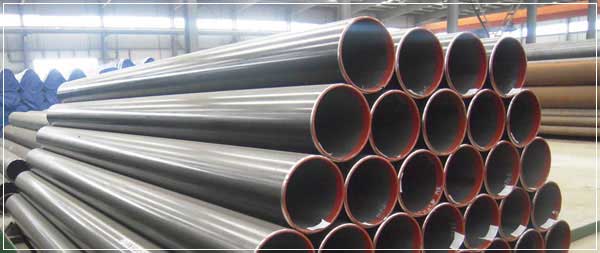
Недоліки сталевих труб для газу:
- - схильність до корозії, що приводить до зменшення внутрішньої порожнини;
- - порівняно велику вагу;
- - трудомісткий і витратний в часі монтаж;
- - висока теплопровідність, що приводить до утворення конденсату на зовнішній поверхні, в слідстві чого починається процес корозії;
- - зварене з'єднання - найвразливіше для іржі;
- - обмеження в довжині виробів, що постачаються;
- - обмежена гнучкість.
монтаж газопроводу
Вимоги до газопроводу:
- - положення повинно повністю відповідати проекту;
- - на газопроводі повинна бути повністю збережена ізоляція, якою оснащені сталеві газові труби;
- - всі з'єднання повинні бути стовідсотково герметичними, що не допускають витік;
- - труби повинні щільно прилягати до основи;
- - ліжко повинна бути збережена;
- - обов'язковими елементами є водоотводчікі (для відведення конденсату з зовнішньої поверхні) і компенсатори (для нейтралізації лінійного розширення труби).
Траншею під газопровід не можна готувати заздалегідь. Її дно повинно бути очищено від сміття та каміння. Газопровід монтують з окремих елементів, які зварюються поза траншеї. При опусканні окремих елементів в траншею не допускаються удари об стінки або дно. Якщо газопровід прокладається взимку, то траншея повинна бути вирита до НЕ промерзлого грунту безпосередньо перед укладанням елементів. На скелястих грунтах потрібно підсипка з піску (приблизно 200 мм).

Ізоляція зовнішньої поверхні сталевих труб
Якщо трубопровід покладений в землю, він піддається впливу корозії і блукаючих струмів, що руйнують його стінки. Щоб продовжити термін служби труб, вони покриваються різними антикорозійними ізоляційними матеріалами ще на заводі. При транспортуванні і монтажі слід звертатися з трубами обережно, так як відновити ізоляцію в польових умовах досить складно.

Під час монтажу все-таки необхідні роботи по ізоляції швів, які утворюються після зварювання окремих елементів трубопроводу. Для цієї мети використовуються різні антикорозійні покриття, виготовлені на основі бітуму, і рулонні матеріали (крафт - папір або полімер). Залежно від властивостей грунту, антикорозійна ізоляція може бути нормальною, посиленою або захисним покриттям дуже посиленого.
Труба очищається до металевого блиску. Потім на неї наноситься грунтовка. Бітумну мастику готують в Бітумоплавильні котлах і наносять на ґрунтовку за допомогою лійки, поки вона гаряча. Поверх мастики внахлест намотується рулонний ізоляційний матеріал.
Внутрішня ізоляція сталевих труб
Для внутрішньої ізоляції сталевих труб найчастіше використовують епоксидні матеріали. Вони запобігають корозії внутрішньої поверхні і виникнення інших відкладень, зберігаючи пропускну здатність незмінною.
Трубопровід для транспортування газу полягає не тільки зі сталевих труб, а й з кранів, гідравлічних затворів, компенсаторів і конденсатосборщіков. Крани виготовляються з чавуну, стали і бронзи з діаметром 15 - 700 мм. Затвори виконують функції пристроїв, що відключають - для відключення газу в трубопровід подається вода, яка заповнює нижню частину затвора, перериваючи надходження газу. Щоб знову підключити газ, вода видаляється за допомогою продувки. Випробування на міцність затвори проходять на заводі.
Компенсатори монтуються в колодязі і з'єднуються з газопроводом. При мінусових температурах їх перед установкою розтягують, при плюсовій - стискають. Конденсатосборщікі збирають з газопроводу конденсат, тому монтуються в нижніх його точках. Періодично воду з цих пристроїв необхідно видалити.

Матеріали і технічні вироби, що використовуються в системах газопостачання, перш за все повинні бути надійними і відповідати вимогам державних стандартів або технічних умов, затверджених в установленому порядку і пройшли державну реєстрацію відповідно до ГОСТ 2.114-70 * (XXXXXX). Традиційно для газопроводів застосовуються сталеві труби. Але останнім роки все активніше використовуються поліетиленові, вініпластовие і азбоцементні труби, особливо для транспортування попутних газів з вмістом понад 3% сірководню, а також при дуже високу корозійну активність грунтів і при наявності блукаючих струмів.
Для підземних міжселищних газопроводів тиском до 0,6 МПа і підземних газопроводів тиском до 0,3 МПа, що прокладаються на території поселень, застосовують поліетиленові труби відповідно до Правил безпеки Госгортехнадозора РФ ПБ 12-529-03. Також допускається прокладка газопроводів з поліетиленових труб тиском 0,3-0,6 МПа на території поселень з одно-, двоповерхової і котеджної забудовою з чисельністю до 200 жителів. На території міст і промислових підприємств, насичених інженерними комунікаціями, газопроводи з НЕ металевих труб не будуються.
На що застосовуються труби повинні бути видані сертифікати заводів-виготовлювачів або довідки з випискою з сертифікатів, що підтверджують їх відповідність вимогам гл. 11 СНиП 2.04.08-87 (XXX). При відсутності документів проводяться хімічний аналіз і механічних випробування зразків, узятих від кожної партії труб однієї плавки, що підтверджують відповідність якості стали чинними вимогами. Якщо встановити приналежність труб до однієї плавці неможливо, аналіз і випробування слід провести на зразках від кожної труби.
Сталеві труби. Відповідно до рекомендацій СНиП 2.04.08-87 для будівництва систем газопостачання слід застосовувати труби, виготовлені з вуглецевої сталі звичайної якості по ГОСТ 380-71 або якісної сталі по ГОСТ 1050-74, добре зварюється і містить не більше 0,25% вуглецю, 0,056% сірки і 0,046% фосфору.
Сталеві труби випускаються 2 видів: зварні (прямо-і спіральношовні) і безшовні (тепло-, гарячо-або холоднодеформовані). Для будівництва газопроводів застосовуються труби, що задовольняють вимогам СНиП 2.04.08-87 (табл. 5.5). Сталеві труби для зовнішніх і внутрішніх газопроводів - груп В і Г, виготовлені із спокійної маловуглецевої стали групи В по ГОСТ 380-71 * не нижче 2-ї категорії (для газопроводів діаметром понад 530 мм при товщині стінки труб більше 5 мм - не нижче 3 -й категорії) марок Ст2, СтЗ, а також Ст4 при вмісті в ній вуглецю не більше 0,25%; стали марок 08, 10, 15, 20 по ГОСТ 1050-74 *; низьколегованої сталі марок 09Г2С, 17ГС, 17ПС по ГОСТ 19281-73 * не нижче 6-ї категорії; стали 10Г2 за ГОСТ 4543-71 *. У ряді випадків допускається застосування труб із напівспокійної і киплячої сталі:
- для підземних газопроводів в районах з розрахунковою температурою зовнішнього повітря до -30 ° С включно;
- для надземних газопроводів в районах з розрахунковою температурою зовнішнього повітря до -10 ° С (з напівспокійну і киплячої сталі) і -20 ° С включно (з напівспокійну стали);
- для внутрішніх газопроводів тиском не більше 0,3 МПа (3 кгс / см 2 ) З зовнішнім діаметром не більше 159 мм і товщиною стінки труби до 5 мм включно, якщо температура стінок труб в процесі експлуатації не буде нижче 0 ° C;
- для зовнішніх газопроводів труби діаметром не більше 820 мм (з напівспокійну стали) і 530 мм (з киплячою стали) і товщиною стінок не більше 8 мм.
У районах з температурою зовнішнього повітря до -40 ° С для зовнішніх підземних газопроводів допускається використовувати труби з напівспокійної сталі діаметром не більше 325 мм і товщиною стінки до 5 мм включно, а для зовнішніх підземних і надземних газопроводів - з напівспокійну і киплячої сталі діаметром не більше 114 мм і товщиною стінки до 4,5 мм.
Для виготовлення відводів, з'єднувальних частин і компенсуючих пристроїв газопроводів середнього тиску не рекомендується застосовувати труби з напівспокійної і киплячої сталі. Для зовнішніх і внутрішніх газопроводів низького тиску, В тому числі для їх гнутих відводів і сполучних частин, допустимо використовувати труби груп А-В з спокійною, напівспокійну і киплячої сталі марок Ст1, по Ст3 "Ст4 1-3-ї категорій груп А-В по ГОСТ 380-71 * і 08, 10, 15, 20 по ГОСТ 1050-74.
Для ділянок, що зазнають вібраційних навантажень (з'єднаних з джерелами вібрації в ГРП, ГРУ, компресорних станціях та ін.), Повинні застосовуватися сталеві труби груп В і Г, виготовлені із спокійної сталі з вмістом вуглецю не більше 0,24% (Ст2, СтЗ НЕ менше 3-ї категорії по ГОСТ 380-71, 08, 10, 15 по ГОСТ 1050-74).
Мал. 5.3. типи зварних з'єднань: А - зварений V-подібний стик; б - зварений стик з циліндричним підкладним кільцем; в - зварений стик з фасонним підкладним кільцем. 1 - газопровід; 2 - скошена кромка труби; 3 - притуплення кромки; 4 - зварювальний прихватка; 5 - циліндричний подкладное кільце;
6 - буртик кільця; 7 - фасонне подкладное кільце.
Труби, що відповідають ГОСТ 3262-75, застосовуються при спорудженні зовнішніх і внутрішніх газопроводів низького тиску з умовним діаметром до 80 мм включно. Ці ж труби вищої категорії якості з умовним діаметром до 32 мм включно допустимі для імпульсних газопроводів тиском до 0,6 МПа (6 кгс / см 2), при цьому гнуті ділянки імпульсних газопроводів повинні мати радіус шва не менше 2Dy, а температура стінки труби в період експлуатації - не нижче 0 ° С.
Труби безшовні (ГОСТ 8731-87 і ГОСТ 8733-87) застосовні для газопроводів рідкої фази ЗВГ, а електрозварні спіралешовні - для прямих ділянок газопроводів. При цьому труби по ГОСТ 8731-87 допустимі до застосування при 100% -му контролі металу труб неруйнівними методами.
З'єднання сталевих труб повинно проводитися, як правило, зварюванням. Зварене з'єднання повинно бути рівноміцним основному металу труб або мати гарантований заводом-виробником (згідно ГОСТ або ТУ) коефіцієнт міцності. Труби за ГОСТ 3262-75 *, зварні шви яких не мають характеристики міцності зварного з'єднання, допускається застосовувати для газопроводів низького тиску.
Основні характеристики труб наведені в табл. 5.8.
Труби з кольорових сплавів. Імпульсні газопроводи для приєднання контрольно-вимірювальних приладів і приладів автоматики повинні бути, як правило, виготовлені зі сталевих труб для газопроводів відповідного тиску. Однак для їх підключення допускається застосовувати мідні, круглі, тягнуті, холоднокатані труби загального призначення відповідно до вимог ГОСТ 617-72 з міді марок Ml, Mlp, M2, М2р, МОЗ, МЗР по ГОСТ 859-78, томпаку марки Л96 по ГОСТ 15527 -70. Зовнішній діаметр названих труб - 3-30 мм, товщина стінок - 0,5-5,0 мм. Допускаються до застосування тягнені, холоднокатані латунні труби (латунь марок Л63 і Л68) загального призначення (ГОСТ 494-76). Тягнені і холоднокатані труби випускаються в наступних виконаннях: м'які М і напівтверді ПТ (зі знятими внутрішніми розтягують напруженнями), зовнішній діаметр - 3-60 мм, товщина стінки - 0,5-5,0 мм.
Знаходять застосування катані і тягнені труби з алюмінію АД0, АД1 і алюмінієвих сплавів марок АМц, АМг2, АМгЗ, АМг5, АМгб, АВ, Д1, Д16 по ГОСТ 18475-82. Залежно від матеріалу труби виготовляють відпалених М (ПЕКЛОМ, АД1М, АМцМ, АМГ2М, АМгЗМ, АМГ5М, АМгбМ, АВМ, Д1М, Д16М), загартованими і постареним Т (АВТ, Д1Т, Д16Т), з зовнішнім діаметром 6-120 мм і товщиною стінки 0,5-5,0 мм.
Гумової й гумовотканинні рукава. При експлуатації установок, що використовують газове паливо, Широко застосовують гнучкі газопроводи: на газонаповнювальних станціях (ДПС) (при зливі газу із залізничних цистерн), наповненні газом автоцистерн, зливі газу в групові резервуарні установки, при заміні балонів. Гумової й гумовотканинні рукава забезпечують менший термін безаварійної роботи, так як з часом фізичні і механічні властивості гуми і тканини змінюються, аж до втрати еластичності.
Гумової й гумовотканинні рукава, призначені для використання в системах газопостачання, повинні вибиратися відповідно до рекомендацій, викладених в табл. 5.7-5.8. При виборі рукавів слід враховувати їх стійкість до транспортується середовищі при мінімальній температурі експлуатації. Рукава всіх класів повинні мати на обох кінцях спеціальні пристосування різної конструкції для приєднання до трубопроводів і штуцерів судин і апаратів.
При визначенні довжини рукавів слід мати на увазі можливість усадки, яка може досягти 3-4% від загальної довжини рукава. Кінці труб під рукав повинні бути прямими і не менше ніж подвійний діаметр рукава
З'єднання повинні витримувати гідравлічний тиск, Вдвічі перевищують робочий тиск в системі, і пробне пневматична, що дорівнює робочому тиску в системі.
Поліетиленові труби. Згідно СНиП 42-01-02 ці труби можуть застосовуватися для газопостачання селищ і сільських населених пунктів, куди подають природні гази газових і газоместорожденій, що не містять ароматичних і хлорованих вуглеводнів. Їх виготовляють з поліетилену низького тиску з маркуванням «ГАЗ» відповідно до ТУ 6-19-051-538-85. Для газопроводів низького і середнього тиску застосовуються труби типу С.
З'єднання поліетиленових труб - зварювання, роз'ємні з'єднання поліетиленових зі сталевими, з компенсаторами і запірною арматурою - на втулках під фланець, що розміщується в колодязі, або в разі нероз'ємних з'єднань - розтрубно-контактним способом в грунті.
Глибина закладки поліетиленових труб - не менше 1 м до верху труби. Нормативні відстані до споруд і будівель приймаються відповідно до СНиП 2.07.01-86. Не допускається застосування поліетиленових труб для газопроводів:
- в районах з розрахунковою температурою нижче -40 ° С,
- в сильноздимистих, скельних грунтах,
- в грунтах II типу просідання,
- в районах підроблюваних територій
- в районах з сейсмічністю понад 6 балів.
Забороняється надземна і наземна прокладка газопроводів з поліетиленових труб, а також в колекторах, каналах і всередині будівель.
Сполучні і фасонні частини, вузли і деталі труб. Для газопроводів і газового обладнання застосовуються заводські з'єднувальні частини та деталі, виготовлені з ковкого чавуну або з спокійної сталі (литі, ковані, штамповані, гнуті або зварні) відповідно до державних і галузевих стандартів (табл. 7.11).
Допускаються до використання сполучні частини і деталі, виконані з урахуванням технічних вимог одного із стандартів на відповідну з'єднувальну частину або деталь, а також виготовлені на базах будівельних організацій за умови неруйнівного контролю зварних з'єднань неруйнівними методами.
Матеріал для виготовлення сполучних частин і деталей - сталеві безшовні та прямошовні зварені труби або листовий прокат, метал яких відповідає технічним вимогам, передбаченим пп. 11.5-11.12 СНиП 2.04.08-87.
Фланці приєднання до газопроводів повинні відповідати вимогам ГОСТ 12820-80 * і ГОСТ 12821-80 *.
1 - труба; 2 - отвір для болта; 3 - фланець; 4 - зварний шов; 5 - приварне кільце; 6 - бурт.
Для поворотів газопроводу застосовують нормалізовані гнуті відводи з безшовних труб (на кути 15, 30, 45, 60, 75 і 90 °) радіусом (3, 4 і 6) D н (для Dy ≤ 400 мм), крутовигнуті (45, 60, 90 °) радіусом (1 ÷ 5) D н (для Dy ≤ 500 мм) або гнуті відводи - різьбові косинці з ковкого чавуну з Dy< 50 мм.
На зовнішніх газопроводах фланцеві з'єднання застосовуються для установки засувок, кранів та іншої арматури. Різьбові з'єднання використовують в місцях установлення кранів, пробок, муфт на конденсатозбірниках і гідрозатворів, запірної арматури на надземних вводах газопроводів низького тиску та приєднання КВП. На внутрішніх газопроводах фланцеві і різьбові з'єднання допускаються тільки для приєднання запірної арматури, КВП і обладнання. Розумні з'єднання повинні бути доступні для огляду і ремонту. для різьбових з'єднань найбільш поширеною є циліндрична трубне різьблення (ГОСТ 6357-81). В окремих випадках застосовується метрична різьба (ГОСТ 24705-81) або конічна (ГОСТ 6111-52 *).
Ущільнювальні матеріали. Для ущільнення фланцевих з'єднань слід застосовувати прокладки, виготовлені з матеріалів, перелічених у табл. 5.10. Прокладки з пароніту просочуються циліндровим маслом і покриваються графітовим порошком. Допускається застосовувати прокладки з іншого ущільнюючого матеріалу, що забезпечує не меншу герметичність в порівнянні з матеріалами, наведеними в табл. 5.10 (з урахуванням параметрів середовища, тиску та температури). Для додання прокладкам вогнестійких властивостей можна використовувати металеві гофровані прокладки.
Для ущільнення різьбових з'єднань слід застосовувати лляну чесання пасмо (ГОСТ 10330-76 **), промазану суриком або свинцевими білилами; фторопластовий ущільнювач у вигляді стрічки або шнура.
Для складання різьбових з'єднань може бути використана фітингових паста заводського виготовлення. Фітингових пасту і полімерні стрічки рекомендується застосовувати поблизу котлоагрегатів, пальників при температурі вище 60 ° С.
Для ущільнення сальників, футлярів і місць проходу газопроводу через стіни і фундаменти споруд використовують смоляну або бітумоізолірованную конопляну пасмо.
Сальникові набивки й змащення. Матеріал для виготовлення сальникової набивки вибирають по ГОСТ 5152-84. Технічні характеристики набивань, найбільш широко використовуваних в системах газопостачання, наведені в табл. 5.11.
Для вузлів тертя без води при температурі до 115 ° С застосовуються мастила на основі консталіна - пластичної вогнетривкої мастила, що складається з нафтового масла, загущенного натрієвими солями вищих жирних кислот.
Для бронзових пробочних кранів застосовується термостійкий мастило наступного складу,% за масою: мелена слюда - 2; натриевое мило - 35 ± 4; машинне масло - 58 ± 5. Для короткочасного захисту від корозії оброблених металевих поверхонь застосовують солідол або спеціальні консерваційні мастила і пасти.
Зачистка металевих поверхонь від корозії проводиться гасом або порошком, приготованим з 50 г тонкоизмельченного мила і 50 г трепелу (пухкої або слабо зцементованою тонкопорістой опалової осадової породи, що використовується в сухих будівельних сумішах в якості активного мікронаповнювача). Промивання деталей - авіаційним бензином, уайт-спіритом або ацетоном.
Для зберігання на складі найкращі результати забезпечує гарматна мастило ПВК (ГОСТ 19537-83), що виготовляється з нафтового масла, загущенного петролатумом і церезином з антикорозійними присадками, або консерваційні масло.
Трубопровідна запірна арматура. Під цією назвою мається на увазі широкий спектр різноманітних пристроїв, призначених для управління струмами середовища (рідкої, газоподібної, газожидкостной і т.п.), що транспортується по трубопроводах. За допомогою арматури виробляються включення / відключення подачі, зміна тиску або напрямки газового або рідинного потоків, контроль рівнів рідин, автоматичне видалення газів і рідин.
Основні частини арматури - запірний або дросельне пристрій і привід. Вони укладені в закритий корпус, всередині якого переміщається затвор. Корпус оснащений приєднувальними кінцями, якими він герметично кріпиться на трубопроводі. Переміщення затвора всередині корпусу щодо його сідел змінює гідравлічний опір проходу - фактично його площа.
Сідло - частина внутрішньої поверхні корпусу або деталь, з якої сполучається затвор при закритому проході. арматурні пристрої в залежності від призначення називаються:
- запірними - призначеними для герметичного роз'єднання
- частин трубопроводу або апарата;
- дросельними - призначеними для точного регулювання площі проходу - гідравлічного опору.
Класифікація арматури. Згідно з чинним ГОСТ 356-80, арматура і сполучні частини трубопроводів характеризуються умовним, пробним і робочим тиском. Залежно від умовного тиску арматуру можна розділити на три основні групи:
- низького тиску (ру - до 1,0 МПа);
- середнього тиску (ру \u003d 1,6 ÷ 6,4 МПа);
- високого тиску (ру \u003d 6,4 ÷ 40,0 МПа).
умовний тиск - параметр, який гарантує міцність арматури і враховує як робочий тиск, так і робочу температуру. Умовний тиск відповідає допустимому для даного вироби робочому тиску при нормальній температурі - при підвищенні температури властивості конструкційних матеріалів погіршуються. Тиску, які вказуються для арматури, завжди є надлишковими (обумовлюються тільки абсолютні). Робоча температура - гранична тривала температура робочого середовища без урахування короткочасних підвищень, що допускаються технічними умовами. Допускається перевищення фактичного робочого тиску над зазначеним в стандарті або каталозі на 5%.
При виборі матеріалу арматури для газопостачання слід враховувати умови експлуатації, тобто тиск газу і температуру відповідно до даних табл. 5.14.
Основний розмірний ряд арматури - діаметр умовного проходу Dy - номінальний внутрішній діаметр трубопроводу, на якому встановлюють дану арматуру. Різні типи арматури при одному і тому ж умовному проході можуть мати різні прохідні перетини. Не слід плутати умовний прохід з прохідним перетином в арматурі, в той же час умовний прохід арматури не збігається і з фактичним прохідним діаметром трубопроводу.
Залежно від призначення трубопровідна арматура підрозділяється на наступні класи:
I - запірна, призначена для повного перекриття потоку середовища;
II - регулююча, керуюча тиском або витратою середовища шляхом зміни прохідного перетину;
III - запобіжна, що забезпечує частковий випуск середовища в разі потреби або повне припинення її подачі для запобігання підвищенню тиску, що загрожує міцності системи, а також запобігає неприпустимий з технологічних міркувань зворотний потік середовища;
IV - резервуарна, контрольна та інша арматура різного призначення.
Кожен клас за принципом дії поділяється на дві групи (табл. 5.15), а класи і групи діляться за типами арматури (табл. 5.16). Крім того, арматура кожного типу має додаткові характеристики за призначенням і конструктивним виконанням.
Способи приєднання арматури. Основні способи - фланцеве, муфтове, цапфових, зварне (нерознімне). Найчастіше застосовується фланцевая арматура, переваги якої очевидні: можливість багаторазового монтажу і демонтажу на трубопроводі, надійність герметизації стиків і можливість їх підтяжки, велика міцність і придатність для широкого діапазону тисків і проходів. До недоліків відносяться можливість ослаблення затяжки і втрата герметичності, порівняльна трудомісткість збирання та розбирання, великі розміри і маса.
Для малої литий арматури з умовними проходами до 50 мм (особливо чавунної) часто застосовуються муфтові з'єднання, основна сфера застосування яких - арматура низьких і середніх тисків.
Для малої арматури високого тиску, виготовленої з поковок або прокату, застосовується цапфових з'єднання з зовнішньою різьбою під накидну гайку.
Зварні з'єднання забезпечують абсолютну довготривалу герметичність з'єднання, зниження загальної маси арматури і трубопроводу. Недолік зварних з'єднань - складність демонтажу і заміни арматури.
Поширені типи запірної арматури. Залежно від характеру переміщення запірних елементів запірна арматура ділиться на наступні типи (див. Табл. 5.17):
- засувки;
- крани;
- клапани;
- затвори поворотні.
Засувки - запірні пристрої, які перекривають прохід переміщенням затвора в напрямку, перпендикулярному до руху потоку середовища. У порівнянні з іншими видами запірної арматури засувки мають наступні переваги:
- незначним гідравлічним опором при повністю відкритому проході;
- відсутністю поворотів потоків;
- можливість застосування для перекриття
- потоків середовища великої в'язкості;
- простотою обслуговування;
- можливістю подачі середовища в будь-якому напрямку.
До недоліків, загальним для всіх конструкцій засувок, відносяться:
- неможливість використання для середовищ з кристалічними включеннями;
- невеликий допустимий перепад тиску на затворі (в порівнянні з вентилями);
- невисока швидкість спрацьовування затвора;
- можливість отримання гідравлічного удару в кінці ходу;
- велика висота;
- труднощі ремонту зношених поверхонь ущільнювачів при експлуатації;
- неможливість застосування постійного мастила ущільнюючих поверхонь сідла і затворів.
При закриванні засувок запірний елемент не зустрічає помітного протидії середовища, так як рухається перпендикулярно потоку, тобто необхідно подолати тільки тертя. Площа поверхонь ущільнювачів засувок невелика, і завдяки цьому засувки забезпечують надійну герметичність.
Різноманітні конструкції засувок можна в загальному випадку розділити на два типи: клинові і паралельні. У свою чергу клинові засувки поділяються на засувки з цільним, пружним і складовим клинами, а паралельні - на однодискові (шиберні) і дводискові. У засувках, призначених для роботи при високих перепадах тиску на затворі, для зменшення зусиль відкривання / закривання повна площа проходу виконується меншою, ніж площа перерізу вхідних патрубків (суджений прохід).
Залежно від конструкції систем «гвинт-ходова гайка» разлічаютcя засувки з висувним і з невисувними шпинделем. Останні повинні мати покажчики ступеня відкриття.
затвор клинових засувок має вигляд плоского клина, а сідла або поверхні ущільнювачів, паралельні ущільнюючих поверхонь затвора, розташовані під кутом до напрямку переміщення затвора. Така конструкція забезпечує герметичність проходу в закритому положенні і незначність зусилля ущільнення.
У паралельних засувках ущільнювальні поверхні паралельні один одному і розташовані перпендикулярно до напрямку потоку робочого середовища. Перевагами засувок цієї конструкції є простота виготовлення затвора (диска або шибера), простота збірки і ремонту і відсутність заїдань затвора в закритому положенні. Але паралельні засувки вимагають значних зусиль закривання / відкривання і характеризуються сильним зносом ущільнювальних поверхонь.
Більшість засувок можна встановлювати на горизонтальних і вертикальних газопроводах в будь-якому положенні, крім положення шпинделем вниз. Положення засувок з пневматичним і електричним приводом регламентується особливо.
Крани - запірні пристрої, в яких рухома деталь затвора (пробка) має форму тіла обертання з отвором для пропуску потоку і при перекритті потоку обертається навколо своєї осі.
Залежно від форми поверхонь ущільнювачів затвора крани підрозділяються на три типи: конічні, циліндричні (для газового обладнання не застосовуються) і кульові (зі сферичним затвором). Крім того, конструкція кранів може варіюватися за іншими параметрами, наприклад, за способом створення тиску на ущільнюючих поверхнях, за формою прохідного вікна, по числу проходів, по типу управління і приводу, за конструкційних матеріалів і т.д.
Конусность пробки (корпусу) конічних кранів задається в залежності від антифрикційних властивостей застосовуваних матеріалів і дорівнює 1: 6 або 1: 7. За способом створення питомої тиску між корпусом і пробкою для забезпечення необхідної герметичності в затворі крани з конічним затвором поділяються на такі типи: натяжні, сальникові з мастилом і з притиском пробки.
До групи натяжних кранів входять широко поширені муфтові крани з різьбовій затягуванням, прості за конструкцією і зручні в регулюванні зусилля затяжки. Сальникові крани характерні тим, що необхідні для герметичності питомі тиску на конічних ущільнювальних поверхнях корпусу і пробки створюються при затягуванні сальника. Зусилля затягування передається на пробку, притискаючи її до сідла. Сальникові крани зі змазкою застосовуються для зниження зусиль управління при середніх і великих діаметрах умовного проходу, питомих тисків на ущільнюючих поверхнях і запобігання задирания контактуючих поверхонь.
Широке поширення отримали кульові крани, що володіють всіма перевагами конічних (простотою конструкції, прямоточні і низьким гідравлічним опором, постійністю взаємного контакту поверхонь ущільнювачів), в той же час вигідно відрізняються:
- меншими габаритами;
- підвищену міцність і твердість;
- підвищеним рівнем герметичності, обумовленим конструкцією (поверхня контакту поверхонь ущільнювачів корпусу і пробки повністю оточує прохід і герметизує затвор крана);
- меншою трудомісткістю виготовлення (відсутність трудомісткою механічної обробки і притирання ущільнюючих поверхонь корпусу і пробки).
Кульові крани, незважаючи на різноманітність конструкцій, можна розділити на два основних типи: крани з плаваючою пробкою і крани з плаваючими кільцями.
Мал. 5.9. Запірний клапан серії 19041 фірми FAS (Німеччина). Характеристики: Dу - 15-200 мм (DIN 2635), ру - до 4 МПа, діапазон робочих температур - -40 ... + 70 ° С. Матеріал корпусу - GS-C25, пробки і шпинделя - нержавіюча сталь. На схемі показані: 1. Корпус; 2. Кришка; 3. Пробка; 4. Шпиндель; 5. Рукоятка; 6. Ущільнення; 7. Шпилька; 8. Гайка; 9. Прокладка; 10. Напрямна; 12. Ущільнення пробки.- Клапани - запірна трубопровідна арматура з поступальним переміщенням затвора в напрямку, що збігається з напрямком потоку середовища. Переміщення затвора здійснюється вгвинчуванням шпинделя в ходову гайку. В основному клапани призначені для перекривання потоків, але часто на їх основі створюються дросселирующие пристрої з будь-якими витратними характеристиками.
У порівнянні з іншими видами запірної арматури клапани мають такі переваги:
можливістю роботи при високих перепадах тисків на золотнику і при великих робочих тисках;
- простотою конструкції, обслуговування і ремонту;
- малим ходом золотника (в порівнянні з засувками), необхідним для перекриття проходу (зазвичай не більше 1 / 4Dу);
- невеликими габаритними розмірами і масою;
- герметичністю перекриття проходу;
- можливістю використання в якості регулюючого органу та установки на трубопроводі в будь-якому положенні (вертикальному / горизонтальному);
- безпекою щодо виникнення гідравлічного удару.
Для перекриття потоку в трубопроводах з малим умовним проходом і високими перепадами тиску клапани - єдиний прийнятний вид запірної арматури. Перевага клапанів перед засувками ще і в тому, що в них ущільнення золотника легко може бути виконано з гуми або пластмаси, при цьому зусилля герметизації значно знижується, а корозійна стійкість ущільнення - підвищується. До загальних недоліків клапанів відносяться:
- високий гідравлічний опір;
- неможливість їх застосування на потоках сильно забруднених середовищ;
- велика будівельна довжина (в порівнянні з засувками і дисковими затворами);
- подача середовища тільки в одному напрямку, заданому конструкцією вентиля;
- порівняно висока вартість.
Однак для управління потоками з високими робочими тисками, а також низькими або високими температурами робочої середовища клапанів немає альтернатив.
Класифікація численних конструкцій клапанів може бути проведена за кількома ознаками:
- по конструкції - прохідні, кутові, прямоточні і змішувальні вентилі;
- за призначенням - запірні, запірно-регулюючі та спеціальні;
- по конструкції дросельних пристроїв - з профільованими Золотниками і голчасті;
- по конструкції затворів - тарілчасті і діафрагмові;
- за способом ущільнення шпинделя - сальникові і сильфонні.
Характеристики клапанів, що застосовуються в системах газопостачання, наведені в табл. 5.15.
Вибір арматури. При проектуванні і будівництві систем газопостачання, а також при Газообладнання агрегатів і апаратів на промислових і комунально-побутових підприємствах вибір арматури визначається проектною організацією з урахуванням фізико-хімічних властивостей, тиску і температури робочого середовища і навколишнього повітря, а також вимог діючих технічних нормативних документів.
Конструкція і матеріали застосовуваної арматури повинні забезпечувати надійну і безпечну експлуатацію систем при заданих параметрах з урахуванням вибухо-і пожежонебезпеки горючих газів. Електрообладнання приводів і інших елементів трубопровідної арматури має відповідати вимогам вибухобезпеки, зазначеним в Правилах Пристрої електроустановок (ПУЕ).
Основні вимоги, що пред'являються до запірної арматури, яка встановлюється на газопроводах:
- міцність і герметичність відключення незалежно від напрямку руху газів, що відповідають вимогам ГОСТ 9544-2005;
- корозійна стійкість;
- вибухобезпечність;
- надійність роботи в експлуатації і простота обслуговування;
- швидкість закривання і відкривання;
- мінімальний гідравлічний опір проходу газу;
- можливість регулювання проходу газу;
- невелика будівельна довжина;
- невеликі маса і габаритні розміри.
Міцність арматури визначається в основному робочим тиском і температурою, які можуть мати будь-які значення в широкому діапазоні. При виборі арматури для газопроводів слід враховувати наступні властивості металів:
- Гази мало або не впливають на чорні метали, тому арматура може бути сталевий і чавунною. При цьому слід враховувати, що через недостатньо високих механічних властивостей чавунна арматура може застосовуватися при тиску не більше 1,6 МПа. При використанні чавунної арматури важливо виключити умови, при яких її фланці працювали б на вигин.
- Технічними нормамім обмежено застосування чавунної арматури у вибухонебезпечних умовах;
- Гази, що містять значні кількості сірководню (більше 2 г на 100 м 3 ), Досить активно впливають на бронзу та інші мідні сплави, тому не рекомендується використовувати арматуру з бронзовими поверхнями ущільнювачів (кільцями). Також слід мати на увазі, коли поверхні ущільнювачів сідла і затвора проточені на відповідних деталях з чорних металів (тобто без вставних кілець з нержавіючої сталі і кольорових металів), ці поверхні схильні до швидкого зносу в робочих умовах і корозії при складському зберіганні;
- Нержавіючі стали стійки в середовищі газу і при складському зберіганні. Для відповідальної арматури можна рекомендувати вставні кільця ущільнювачів з нержавіючої сталі;
- Ущільнювальні кільця з бабіту можуть застосовуватися для горючих газів для арматури клапанного типу, експлуатованої при невисоких температурах;
- Ущільнювальні кільця з гуми застосовуються в арматурі клапанного типу лише при температурах до 50 ° С і тиску до 1,0 МПа;
При зберіганні і транспортуванні горючих газів потрібна мінімальна теплоємність арматури, щоб при її включенні час охолодження до температури рідини було можливо малим. Корпус арматури повинен мати невелику металоємність при досить високій міцності.
При зберіганні, монтажі та експлуатації трубопровідної арматури необхідно виконувати наступні вимоги:
- перед установкою арматури трубопровід повинен бути ретельно очищений і, піску і окалини;
- арматура з вказівкою напрямку руху середовища (стрілка на корпусі), встановлюється на трубопроводі тільки відповідним чином;
- при монтажі фланцевої арматури необхідно, щоб фланці і отвори болти збігалися з отворами на фланцях арматури; затягувати болти рівномірно і нормальним гайковим ключем;
- місце установки арматури повинно бути освітлено, а проходи між арматурою і будівельними конструкціями - відповідати нормам забезпечення безпечного обслуговування і огляду;
- при гідравлічному випробуванні трубопроводу на міцність затвори арматури повинні бути повністю відкриті;
- забороняється використовувати запірну арматуру в якості регулюючої або дросселирующей;
- забороняється при закриванні і відкриванні арматури застосовувати додаткові важелі;
- зовнішнє різьблення шпинделів необхідно змащувати не рідше 1 разу на місяць;
- зберігати арматуру на складі в упаковці заводу-виготовлювача або в упакованому вигляді (обов'язково з заглушками) на стелажах в сухому приміщенні. При тривалому зберіганні кожні півроку необхідно міняти мастило на оброблених поверхнях виробів і видаляти виявлену бруд або іржу;
- використовувати арматуру строго за призначенням відповідно до вказівок в технічному паспорті, технічних умовах, Стандартах або в особливих умовах замовлення;
- забороняється проводити роботи з усунення дефектів і перебивати сальник при наявності тиску в газопроводі;
- сальникові болти і шпильки підтягувати рівномірно щоб уникнути перекосів;
- при виявленні непереборних нещільності в прокладках (між корпусом і кришкою) і в затворах арматуру необхідно зняти з газопроводу, розібрати і ретельно оглянути. Дефекти на ущільнюючих поверхнях необхідно усунути приточкой або притиранням, якщо можливість подібного ремонту передбачена конструкцією;
- арматура, призначена для відповідальних установок, які перебувають в експлуатації, резерві або ремонті, приймається на облік і реєструється в спеціальному журналі із зазначенням часу установки, виробничого огляду і ремонту, виду ремонту і стану після нього;
- обслуговуючий персонал, який проводить роботи з консервації і розконсервації арматури, повинен мати індивідуальні засоби захисту та дотримуватися вимог протипожежної безпеки.
Арматура загального призначення перед установкою піддається таким випробуванням:
- крани - на міцність і щільність матеріалу деталей водою або повітря тиском 0,2 МПа; на герметичність затвора, сальникових і прокладок ущільнень - повітрям тиском, рівним 1,25 робочого. Крани, розраховані на робочий тиск не менше 0,04 МПа, повинні проходити випробування тиском 0,05 МПа;
- засувки - на міцність і щільність матеріалу водою тиском 0,2 МПа, а також додатково - на щільність повітрям тиском 0,1 МПа; на герметичність затвора - заливанням гасу, при цьому результати випробувань повинні відповідати вимогам для арматури відповідного класу герметичності.
Арматуру загального призначення, що встановлюється на газопроводах середнього і високого тиску, випробовують так:
- крани - на міцність і щільність матеріалу водою тиском, рівним 1,5 максимального робочого, але не менше 0,3 МПа; на герметичність затвора, прокладок і сальникових ущільнень - повітрям тиском, рівним 1,25 максимального робочого;
- засувки та вентилі на міцність і щільність матеріалу - водою тиском, рівним 1,5 максимального робочого, але не менше 0,3 МПа з додатковим випробуванням на щільність повітрям, з одночасною перевіркою герметичності сальникових і прокладок ущільнень; на герметичність затвора - заливанням гасу. При цьому результати випробувань повинні відповідати вимогам для арматури відповідного класу герметичності.
Випробування арматури проводяться при постійному тиску протягом часу, необхідного для ретельного її огляду, але не менше 1 хв. «Потеніе» металу, а також пропуск середовища через нього, сальникові і прокладочні ущільнення, не допускаються.
Пристрої захисту частин газопроводів і арматури від пошкоджень. До таких вузлів відносяться ковери, люки, муфти, компенсатори і футляри. Ковери захищають пристрої газопроводів, що виходять на поверхню землі - крани, пробки, трубки збірників конденсату, гідрозатворів, контрольних провідників, - від механічних пошкоджень. Традиційно ковери і люки виготовляються з чавунними литими корпусами і відкидними кришками, але останнім часом все частіше застосовуються і інші матеріали. Для запобігання осідання ковери і люки встановлюються на бетонні подушки з легкої армировкой. Запобіжні муфти з двох зварювальних полумуфт встановлюють з метою підвищення експлуатаційної надійності газопроводів високого та середнього тиску при невпевненості в зварних швах або їх небездоганності.
Компенсатори застосовуються для зниження напруги, викликаної перепадами температури грунту на фланці чавунної арматури, а також для можливості демонтажу, зміни прокладок і подальшої їх установки. Лінзові компенсатори, що встановлюються на підземних газопроводах в колодязях спільно з арматурою, виконуються з тонколистової сталі у вигляді окремих зварювальних між собою полулінз. Для забезпечення нормальних умов демонтажу і монтажу, а також для зняття температурних напружень з фланців арматури застосовуються двохлінзові компенсатори, що складаються з чотирьох полулінз. Лінзові компенсатори встановлюють в стислому стані з урахуванням їх максимальної компенсує здібності і осьових зусиль. Під максимальної компенсує здатністю компенсатора розуміється двостороннє зміна його довжини. Для багатолінзові компенсатора цю здатність визначають сумою компенсує здібності окремих лінз.
Футляри використовуються для захисту газопроводів від механічних впливів, які перебувають над і під ними споруд і запобігання від попадання в них речовини в разі розриву або нещільності газопроводів. Пристрій простого футляра, службовця для прокладки газопроводу через фундаменти, стіни будівель і споруд, показано на рис. 5.11.
Газорегуляторні пункти (ГРП) промислових і комунально-побутових підприємств споруджуються в окремій будівлі і призначені для харчування газом декількох великих споживачів (цехів, котелень). ГРП з вхідним тиском не більше 0,6 МПа можна розміщувати в прибудовах до промислових будівель I і II ступеня вогнестійкості з виробництвами, віднесеними за пожежною небезпекою до категорій Г і Д. Газорегуляторні установки (ГРУ) і контрольно-регуляторні пункти (КРП) монтують безпосередньо в приміщеннях цехів і котелень, де знаходяться агрегати, що використовують газ.
До складу ГРП (ГРУ, КРП) входять:
- фільтр-очищувач;
- регулятор тиску;
- запобіжні, запірні і стічні пристрої;
- запірна арматура;
- КВП;
- вузол вимірювання витрати газу (лічильник або вимірювальна діафрагма).
Газ початкового тиску через засувку надходить у фільтр, де очищається від механічних домішок. Очищений газ проходить через запобіжний запірний клапан, призначений для відключення подачі газу при аварійному відхиленні (по максимуму і мінімуму) вихідного тиску. Далі газ потрапляє в регулятор тиску, головний вузол будь-якого газорегуляторного блоку. Він знижує тиск газу до заданого і автоматично підтримує його незалежно від зміни витрати газу. Регулятор тиску і запобіжний запірний клапан через імпульсну систему трубопроводів з'єднані з газопроводом вихідного тиску.
Регулююча лінія ГРП має обвідний газопровід (байпас). При виході з ладу будь-якого приладу регулюючої лінії або при проведенні ремонтно-профілактичних робіт закриваються засувки до фільтра і після регулятора, тобто ГРП перекладається на байпасну лінію, на якій встановлені два запірних клапана: перше працює в дросельному режимі, сприймаючи на себе основний перепад тиску, а друге - в режимі клапана, що підтримує постійний заданий вихідний тиск.
Запобіжний скидний пристрій призначений для зниження вихідного тиску газу після регулятора натравлюванням частини газу в атмосферу. Воно повинно налаштовуватися на тиск, менший максимального тиску відсічення запірного клапана. При різкому падінні витрати газу (викликаного, наприклад, відключенням частини агрегатів, що споживають) регулятор не відразу відновлює заданий тиск, і тиск газу в системі газопостачання після регулятора короткочасно підвищується. Скидний клапан і знімає його.
В аварійному режимі скидний клапан не зможе знизити вихідний тиск через малу пропускну здатність. Тиск газу після регулятора буде підвищуватися, поки не досягне тиску відсічення запобіжного запірного клапана, який і відключить подачу газу в ГРП.
ГРП розрахований на автоматичну роботу. Для періодичного контролю роботи приладів і обладнання встановлюються манометри, а для обліку - витратоміри.
У практиці застосовуються ГРП різних типів: одно- і двоступінчасті (послідовно встановлені два регулятора); одинарні, здвоєні і строєні (паралельно встановлені три регулюють лінії). Двоступенева зниження тиску газу застосовують в цілях безпеки і зниження рівня шуму.
Паралельна установка регулюючих ліній виправдана в тому випадку, коли пропускна здатність регулятора тиску не забезпечує необхідної витрати газу або коли витрата газу на підприємстві різко змінюється в межах великих, ніж допустимі зміни пропускної здатності регулятора. При паралельній роботі двох і більше регулюючих ліній ГРП кожна налаштовується на вихідний тиск, трохи відмінне від тиску на сусідній лінії. В цьому випадку лінії включаються в роботу і вимикаються автоматично, в залежності від навантаження.
Для розрахунку і підбору регулятора тиску, а також для визначення параметрів настройки обладнання проводиться гідравлічний розрахунок газопроводів до і після ГРП і визначаються втрати тиску, а настройка - за розрахунковими параметрами і уточнюється в процесі експлуатації.
Мінімальний тиск відсічення газу приймають по мінімальному тиску газу перед пальниками з урахуванням втрат тиску в газопроводах. Пропоновані режими настройки можуть бути скориговані в залежності від тиску газу і типу газових пальників.
Контрольно-распределітельниt пункти (КРП), виконані у вигляді компактного вузла, широко застосовуються в системах автономного газопостачання з малим і середнім споживанням палива.
У конструкцію КРП фірми FAS (Німеччина) включені регулятор тиску і газовий лічильник. Контрольно-розподільний пункт комплектно зібраний в сталевому шафі. Підключення до КРП здійснюється на нижньому боці шафи за допомогою муфт з трубної конічної або циліндричної різьбленням.
Конструкція забезпечує багатоступеневий захист при виникненні нештатних ситуацій:
- При збої електропостачання електромагнітний клапан закривається, припиняючи подачу газу;
- При обриві трубопроводу перекриття газової магістралі здійснюється за допомогою швидкісного клапана;
- При витоку газу в приміщенні, в якому розміщений прилад контролю загазованості, відбувається закриття електромагнітного клапана, припиняючи тим самим подачу газу.
У комплект поставки КРП включені:
- Сталевий шафа;
- Газовий лічильник;
- Регулятор тиску (рис. 5.13);
- муфти;
- Кульові клапани;
- манометр;
- Швидкісний запірний клапан;
- Т-з'єднання;
- Електромагнітний запобіжний клапан.
Зниження шумів в ГРП / КРП. При великих витратах і перепадах тиску в регуляторах можуть виникати шуми і вібрація, інтенсивність яких визначається технологічним режимом роботи устаткування, конструкцією регулюючих пристроїв, акустичними властивостями будівлі ГРП. Шум з будівлі ГРП поширюється в основному через двері, вікна, вентиляційну систему (дефлектори, жалюзі і т.д.) та інші отвори. Основними джерелами шуму є:
- клапанний пристрій регулятора тиску;
- елементи лінії, розташовані після регулятора;
- лінзові компенсатори, круті відводи, врізки, прикриті засувки та ін .;
- виходять зовнішні газопроводи.
- зменшити шум в самому джерелі за рахунок зниження частоти і зон пульсації;
- локалізувати шум за рахунок звукоізоляції джерела шуму;
- підвищити акустичну щільність будівлі ГРП.
Для діючих ГРП доцільно застосовувати пасивний захист, засновану на застосуванні звукопоглинальних матеріалів і конструкцій з метою звукоізоляції найбільш «гучних» вузлів лінії регулювання і підвищення акустичної щільності самої установки ГРП. До цього виду захисту відносяться такі методи:
- нанесення звукопоглинальних покриттів на зовнішню поверхню
- газопроводів і арматури;
- установка звукоізолюючих кожухів;
- облицювання звукопоглинальним матеріалом внутрішніх поверхонь дифузора, парасольки витяжних дефлекторів і прорізів жалюзійних решіток (при цьому необхідно зберегти нормативний повітрообмін вентиляції);
- підвищення акустичної щільності вікон і дверей (подвійні двері з покриттям їх звукопоглинальним матеріалом, подвійні або потрійні вікна з звукопоглинальним матеріалом по периферії прорізів).
Як звукопоглинальних матеріалів в конструкціях можна застосовувати поролон (поропласт поліуретановий), мінераловатні плити, що мають високі ревербераційні коефіцієнти звукопоглинання в високочастотної смузі шумового спектра (0,75-0,98). Як звукопоглинальних покриттів для газопроводів застосовують спеціальні бітумно-гумові мастики.
Особливості газопостачання виробничих дільниць (цехів, майстерень тощо). Виробничі дільниці забезпечуються газом низького або середнього тиску, що визначається видом і кількістю теплогенеруючих агрегатів, а також вимогами «Правил безпеки в газовому господарстві» і СНиП 42-01-2002 «Газорозподільні системи». Загальні елементи схеми цехових газопроводів наступні:
- загальний вимикаючий пристрій на вводі газопроводу в цех незалежно від наявності пристрою, що вимикає на межцеховом газопроводі перед цехом;
- показує манометр на вводі газопроводу в цех після загального пристрою, що вимикає;
- вузол вимірювання витрати газу;
- пристрої, що вимикають на відгалуженнях газопроводів до агрегатів;
- продувальні газопроводи, що забезпечують видалення повітря і газоповітряної суміші під час пуску з усіх внутріцехових газопроводів.
Схема газопостачання цеху (котельні), наведена на рис. 5.14, може застосовуватися для систем газопостачання як низького, так і середнього тиску газу, але після ГРП. Якщо ж системою газопостачання підприємства передбачається установка в цеху ГРУ / КРП, то вона монтується в схему газопостачання цеху між загальним відключає пристроєм і пунктом вимірювання витрати газу.
Введення газопроводу в цех, як правило, здійснюється через стіну будівлі в футлярі (рис. 5.11). Простір між футляром і газопроводом закладається просмоленому лляної пасмом, а з торців заливається бітумом. Футляр призначений для захисту газопроводу від пошкоджень при незначних сезонних або інших деформаціях стіни. Безпосередньо на вводі газопроводу в цех встановлюють загальний вимикаючий пристрій (засувку, кран) в доступному для обслуговування і освітленому місці. Газопроводи в цехах прокладають відкрито по стінах, колонах і інших споруд в місцях, зручних для обслуговування і виключають можливість їх пошкодження цеховим транспортом. Чи не дозволяється прокладати газопроводи через підвальні приміщення, приміщення вибухонебезпечних виробництв, склади вибухонебезпечних та горючих матеріалів, приміщення електророзподільних пристроїв і підстанцій, вентиляційні камери, а також через приміщення, в яких газопровід буде схильний до корозії (приміщення заливки, шлаку, підготовки і ін.). Газопроводи також не слід прокладати в зоні безпосереднього впливу теплового випромінювання топок, в місцях можливого омивання їх гарячими продуктами згоряння або контакту з розпеченим або розплавленим металом.
Газопроводи кріплять спеціальними металевими кронштейнами або підвісками з хомутами. При розташуванні арматури на висоті більше 2 м влаштовуються оглядові майданчики з драбинами або забезпечується дистанційний привід. Якщо ж арматурою користуються зрідка, обслуговуючий персонал може користуватися драбинами. Відстані між газопроводами і стінами цеху вибирають з розрахунку забезпечення легкого огляду і ремонту газопроводів, фланцевих з'єднань, арматури і апаратури. У місцях проходу людей газопроводи повинні прокладатися на висоті не менше 2,2 м, рахуючи від підлоги до низу труби.
У цехах і котелень, як правило, газопроводи прокладають надземно. При розташуванні теплоагрегатів в таких місцях, куди неможливо підвести надземні газопроводи, дозволяється, як виняток, прокладати їх підземно, в бетонних каналах з верхніми знімними плитами. Розміри каналів вибирають з розрахунку можливості монтажу та зручності експлуатації. Вільний простір між каналом і газопроводом для усунення можливості скупчення газу засипають піском. При забезпеченні постійно діючої вентиляції канал з газопроводом можна піском не засинати. Газопроводи в каналах повинні мати мінімальне число зварних з'єднань. Різьбові, фланцеві з'єднання, а також установка запірної арматури в каналах заборонені.
Мал. 5.16. Вузол вводу газопроводу.Газопроводи на кінцевих віддалених ділянках забезпечуються продувними газопроводами, призначеними для звільнення газопроводів від повітря перед пуском теплоагрегатів і витіснення газу повітрям при ремонті, консервації або тривалій зупинці системи газопостачання. До цеховим продувальним газопроводах можуть приєднуватися і продувні газопроводи агрегатів (печей, котлів, сушарок і т. Д.). Продувальні газопроводи виводять з будівель і по зовнішній поверхні стін прокладають не менше ніж на 1 м вище карнизу даху, в місці, де газ безпечно розсіюється. Для виключення можливості попадання опадів кінець газопроводу або загинають, або монтують на ньому захисний зонт.
Труби газопроводи з'єднуються зварюванням. Різьбові і фланцеві з'єднання допускаються в місцях установки арматури, обладнання ГРУ, контрольно-вимірювальних приладів, газових пальників.
Обв'язувальні газопроводи. Вибір схеми обв'язки теплових агрегатів (котлів, промислових печей, сушарок і т.д.) залежить від теплової потужності агрегату, виду і числа пальників, тиску газу в системі, виду пристроїв, що відключають (крани або засувки), а також від типу застосовуваної системи автоматики регулювання і безпеки. Багаторічною практикою доведено, що по надійності відключення (герметичності) крани і клапани ефективніше засувок. Навіть невеликий витік газу відразу ж виявляється по запаху, так як газ, протікаючи через сальник або пробку, як правило, потрапляє в приміщення, а не в топку. Недостатня щільність ж засувки призводить до значних витокам газу в топку, при чому виявити ці витоку без спеціальних приладів практично неможливо.
Варіанти схем обв'язувальних газопроводів вельми різноманітні і сильно прив'язані до типів агрегатів, їх конструкції, що застосовується внутрішнього обладнання (газопальникові пристрої, вузли автоматики, що відключають і лічильні пристрої). Тому в кожній ситуації повинні розроблятися свої, адаптовані до місцевих умов, схеми.
Запобіжні вибухові клапани. Найбільший тиск під час вибуху газоповітряної суміші в замкнутих обсягах, досягає 1 МПа (10 атм) (табл. 5.18). Більшість елементів огороджувальних конструкцій руйнується при тиску до 0,05 МПа: цегляні стіни товщиною 51 см руйнуються при тиску 0,050 МПа, товщиною 38 см - 0,020 МПа, а засклені віконні прорізи - всього при 0,002 МПа. Вибух газоповітряної суміші в топках і газоходах призводить до миттєвого адіабатичному розширення продуктів горіння і зростання тиску, яке може зруйнувати огороджувальні конструкції теплової установки. Освіта вибухонебезпечних газоповітряних сумішей може відбуватися при витоках газу через арматуру, згасанні полум'я пальників в процесі експлуатації і т.п. Небезпечні навіть невеликі витоку газу, так як обсяги топок і газоходів порівняно невеликі.
Для запобігання руйнуванню конструкцій топок і газоходів теплових установок встановлюються запобіжні вибухові клапани, що спрацьовують при тисках менших, ніж руйнують конструкції установок тиску. Ці клапани забезпечують своєчасний скидання тиску продуктів згоряння з камери, де відбувається вибух.
Найбільшого поширення набули клапани розривної, відкидного і скидного типів, що встановлюються на перекриттях і стінах топок і газоходів. Клапани встановлюються в зонах найбільш ймовірного скупчення витоків газу, утворення газових мішків. Їх треба розташовувати так, щоб при спрацьовуванні вибуховою хвилею не уражався обслуговуючий персонал. Якщо це неможливо, необхідно після клапана обладнати захисний короб або козирок, міцно прикріплений до агрегату і відвідний вибуховий вихлоп в сторону. Форма вибухових клапанів повинна бути квадратної або круглої, так як в цьому випадку для розриву мембрани потрібно менший тиск.
Розривної клапан має мембрану з листового азбесту товщиною 2-3 мм, яка руйнується при вибуху. Через утворений отвір продукти згоряння скидаються в навколишнє середовище. Для підвищення міцності і довговічності перед мембраною з боку топки монтують металеву сітку з осередками 40x40 або 50x50 мм. Азбестовий лист і сітку затискають фланцями, які кріплять до металевого короба, Міцно вмонтованому в обмурівку теплового агрегату. Необхідно врахувати, що азбестовий лист може довго працювати при температурі до 500 ° С, тому вибухові клапани встановлюються так, щоб азбестова мембрана не зазнала нагрівання від факела і розпеченій кладки. Клапани розривного типу прості й недорогі.
У відкидних клапанах під час вибуху в топці клапан відкривається і звільняє отвір для викиду продуктів згоряння. З боку топки для запобігання від перегріву клапан футеруют розчином з вогнетривкої глини з азбестом по армуючої металевої сітки. У закритому стані відкидний клапан герметизується по периметру вогнетривкої мастикою.
Скидні клапани являють собою панель, що укладається горизонтально і відкидається під час вибуху. Залежно від місця установки і температурних умов скидна панель може бути виготовлена \u200b\u200bабо з азбестового листа товщиною 8-10 мм, що укладається на металеву сітку і ущільненого по периметру вогнетривкої глиною, або з суміші вогнетривкої глини з азбестового крихтою. Ця панель армується металевою сіткою і може застосовуватися при температурі до 500 ° С.
Розрахунок і підбір запобіжних вибухових клапанів виконується відповідно до діючих СНиП 42-01-2002, «Правилами безпеки в газовому господарстві» і «Правил будови і безпечної експлуатації парових та водогрійних котлів ». У загальному випадку рекомендується орієнтуватися на наступні параметри:
- на 1 м 3 внутрішнього обсягу топки, газоходів і кнурів повинно припадати не менше 0,025 м 2 вибухового клапана, при цьому мінімальна площа поверхні клапана - 0,15 м 2 ;
- для потужного устаткування над топкою повинні бути встановлені вибухові клапани загальною площею поверхні не менше 0,2 м 2 , А на газоходах - не менше двох клапанів з мінімальною сумарною площею поверхні 0,4 м 2 .
Для забезпечення підприємств і населення природним газом розробляються і впроваджуються розгалужені мережі газопостачання, що складаються з газорозподільних пунктів, запірної, вимірювальної і регулюючої арматури та трубопроводів різного тиску. При розведенні трубопроводів застосовуються різні труби для газопроводів.
Застосування сталевих газопровідних труб
Газопровідні металеві труби бувають сталевими (ГОСТ 3262-75) і мідними (ГОСТ Р 52318-2005). Мідні труби малого діаметра застосовуються в обв'язуваннях вузлів нагрівальних приладів, а сталеві труби для газопроводів застосовуються при прокладанні трубопроводів різного тиску від магістральних трубопроводів до розводки газопостачання промислових і побутових газоспоживаючих об'єктів.
Сталеві газопровідні труби з антикорозійним покриттям
Залежно від максимального тиску трубопроводи транспортування природного газу поділяються на такі класи:
- високого тиску (I і II категорії - до 12 і 6 атм. відповідно);
- середнього тиску (до 3 атм.);
- низького тиску (до 0,05 атм.).
Залежно від робочого тиску, зовнішнього діаметра, а також способу прокладки (зовнішні або внутрішні, надземні або підземні), до труб пред'являють різні вимоги до марки стали, товщині стінок, виду антикорозійного покриття.
Труби для магістральних газопроводів виконують зварними по ГОСТ 31447-2012. Товщина стінки розраховується залежно від рівня безпеки траси відповідно до СНиП 2.05.06-85. Магістралі виконуються з труб для газопроводу високого тиску. Трубопроводи середнього тиску прокладаються для постачання багатоквартирних будинків і промислових об'єктів, а низького - при подачі газу на спалювання в пальники.
Антикорозійне покриття буває наступних видів:
- цинкування;
- дво- або тришаровий поліетилен;
- антикорозійна фарба під теплоізоляцію.
Ступінь захисту визначається розташуванням траси і ступенем ризику при порушенні герметичності стінок.
Газопроводи з пластикових труб
Поліетиленові газопровідні труби, марковані жовтої полосойелектромагнітно-акустичної діагностики
Для забезпечення газом невеликих населених пунктів відповідно до СНиП 42-01-02 і ПБ 12-529-03 в газопроводах високого тиску II категорії можуть застосовуватися поліетиленові (ПНД) труби, вироблені за ТУ 6-19-051-538-85. Для трубопроводів середнього і низького тиску допустимо використання труб типу С. Пластикові труби для газопроводу мають обмеження щодо застосування:
- не застосовується в містах та великих населених пунктах;
- газ не повинен містити хлорованих і ароматичних вуглеводнів;
- дозволена тільки зовнішня підземна (глибше 1 м) прокладка трубопроводу;
- сейсмічність району прокладки - не вище 6 балів;
- температура повітря - не нижче 40 ° С;
- обмеження за влучним висловом грунтів.
До переваг поліетилену (ПНД) слід віднести низьку питому вагу і високу корозійну стійкість, що значно полегшує збірку і, при правильному монтажі, дозволяє експлуатувати трубопроводи тривалий період (до 50 років).
Пристрій тришарової поліетиленової труби
Інші пластикові труби застосовуються значно рідше або не застосовуються зовсім. Так, вінілопластовие погано переносять негативні температури (допустиме значення - мінус 5 ° С) і схильні до деформації при навантаженнях, а поліпропіленові для газопроводу не застосовуються зовсім зважаючи на високу газопроникності.
Проектування і будівництво газопроводів
Ультразвуковий безконтактний сканер
Проектування і будівництво газопроводів з металевих і поліетиленових труб виконується відповідно до СНиП 2.04.08-87 і СНиП 42-01-2002. Цими нормативами визначаються схеми трас з транспортування газу при різних умовах і рекомендації по вибору труб і антикорозійного покриття. Будівництво трубопроводів ведеться строго за розробленим проектом і з виконанням вимог СНиП, правил ТБ, а також під авторським наглядом генпроектувальника.
Проектування газопроводів, схема прокладки
Для попередження аварій і техногенних катастроф газотранспортні магістралі періодично потрібно обстежити. Для тестування стану поверхонь застосовуються методи неруйнівного контролю та обладнання зовнішнього і внутрітрубної застосування. До дефектоскопії зовнішнього застосування відносяться вихрострумовий і ультразвуковий.
Внутрішньотрубна діагностика магістральних газопроводів виконується згідно з ГОСТ Р 55999-2014. Найбільшого поширення набув магнітний дефектоскоп, який не тільки виконує діагностику, а й очищає зсередини стінки труб від відкладень. При виявленні дефекту, доступ до ушкодженої ділянки відкривають в строго визначеному місці, що економічно вигідно при підземному прокладанні. Розроблено і вже знаходиться в експлуатації роботизований комплекс електромагнітно-акустичної діагностики. Апарат діагностики всередині трубопроводів переміщається на мобільному телекерованого блоці.
Внутрішньотрубної магнітний дефектоскоп
При розробці, монтажі, експлуатації та дефектоскопії газопроводів необхідно точно дотримуватися всіх нормативних вимог для безперебійного та безаварійного газопостачання споживачів.
Відео: Виробництво сталевих труб для газопроводів на Виксунськом металургійному заводі
Газопровід призначений для транспортування горючої суміші, що відноситься до категорії небезпечних речовин. Дані обставини вимагають особливих матеріалів і умов укладання мереж, що виключають будь-які витоку. Сталеві труби для газопроводів використовуються з початку повсюдної газифікації і по сьогоднішній день. І хоча на сучасному ринку з'явилися їх пластикові аналоги, замінити традиційні вироби вони так і не змогли, незважаючи на те, що мають ряд переваг.
Якими бувають сталеві труби і газопроводи
Для газопровідних мереж випускаються різні види труб. Їх можна розділити на дві основні групи:- безшовні;
- зварні.
Перша група складається з гарячо-і холоднодеформованих, а вироби другої групи відрізняються типом шва - прямим або спіралевидним. При виготовленні труб використовуються різні марки вуглецевої сталі, зазначені в ГОСТ 380-2005. Використання того чи іншого хімічного складу стали, виду і розміру газових труб залежить від декількох факторів:
- тиску в системі - високого, середнього, низького;
- місця розташування трубопроводу - над землею, під землею, під водою, в будівлі;
- призначення мережі - магістральна, розподільна, резервна.
Магістральні газопроводи поділяються на дві категорії. Вони транспортують вибухонебезпечну суміш під тиском до 10МПа на значні відстані. В цьому випадку використовуються сталеві труби великих діаметрів, до яких пред'являються максимально високі вимоги.
Розподільні мережі доставляють газ безпосередньо в точки розбору, тобто до споживача. Такі трубопроводи мають менший діаметр і більш тонкі стінки. Тут є різні нюанси. Наприклад, в квартирах може бути прокладена газопровідна труба - сталева або пластикова у вигляді гнучкого шланга.
Щодо резервної мережі можна сказати, що вона призначається для особливих цілей - стратегічних. До неї пред'являються підвищені вимоги, так як в певних ситуаціях вона може не експлуатуватися.
Газопровідні труби повинні мати сертифікат і супутні документи, в яких вказується виробник і відомості про проведені випробування, спосіб виробництва і марка стали, відмітка про відповідність і номер ГОСТ.
Нормативи по сортаменту
ГОСТ 3262-75
Даний стандарт має відношення до виробництва водогазопровідних труб, призначених для монтажу розподільних систем, що поставляють природний газ під високим тиском (до 1,6 МПа). Умовний діаметр виробів становить до 150мм, довжина - від 4 до 12 метрів.
ГОСТ 8734-75
У нормативному документі вказується сортамент безшовних труб, виготовлених методом холодного формування. Вони витримують тиск, що доходить до 10МПа. Максимальний розмір зовнішнього діаметра - 250мм. Мірна довжина варіює в межах від 4,5 до 9 метрів.
ГОСТ 8732-78
Також визначає сортамент безшовних труб, але не холодно, а горячедеформірованних. Їх зовнішній діаметр має великі розміри - до 530-550мм при товщині стінки - до 75мм. Вироби поставляються довжиною 4-12,5 метрів. Труби допускається встановлювати на магістральних газопроводах високого тиску.
ГОСТ 10704-91
У нормативі вказаний сортамент прямошовних труб. Їх зовнішній діаметр може досягати величини 1420мм. Довжина виробів залежить від їх діаметра. Вона варіює в межах від 2 до 12 метрів.
Переваги і недоліки сталевих газопровідних труб
До позитивних якостей виробів відносяться:
- достатня міцність;
- незначне лінійне розширення;
- здатність протистояти високому тиску;
- стовідсоткова герметичність при правильній стикуванні і відсутності дефектів.
Негативні сторони:
- можливість утворення конденсату через високу теплопровідності;
- висока ймовірність появи процесів корозії;
- відсутність гнучкості;
- трудомісткий монтаж з використанням зварювання.
Вимоги до монтажу
Укладання газопровідних мереж передбачає дотримання певних правил:
- проектне положення повинне дотримуватися неухильно;
- з'єднання необхідно виконувати якісно, \u200b\u200bщоб не допустити витоку газу в період експлуатації;
- труби слід монтувати таким чином, щоб вони щільно прилягали до основи;
- збереження заводської антикорозійної ізоляції є важливим технологічним моментом, від якого залежить несприйнятливість сталевих стінок до впливу блукаючих струмів, а також відсутність процесів іржавіння;
- зварні шви підлягають обов'язковій обробці складами на основі бітуму.
Ізоляція газових труб, призначених для укладання в землю, проводиться в заводських умовах. Її якісне виконання на будівельному майданчику неможливо в силу технологічних особливостей процесу. Залежно від ґрунтових умов, захисне покриття буває звичайним і посиленим.
Газопостачання - це один з найважливіших питань, яке належить розглянути в ході будівництва та благоустрою приватного будинку. Однак це завдання лягає не тільки на плечі власників, але і на спеціалізовані служби, так як прокладка газопроводу і його підключення є проблемою виключно таких служб.
При цьому знати класифікацію систем газопостачання, а також класифікацію окремих складових таких систем необхідно. Наприклад, якими можуть бути газові труби, щоб можна було грамотно висловити свої побажання в цьому питанні.
Які бувають газопроводи
Всі газопроводи діляться на кілька типів залежно від того тиску, який вони відчувають. За цим показником можна виділити наступні типи:
- Високого тиску. У них воно може коливатися від 0,6 до 1,2 мегапаскалей. Ці системи відносять до першої категорії;
- Високого тиску з робочими показниками від 0,3 до 0,6 Мпа. Ці системи відносять до другої категорії;
- Середнього тиску з робочими показниками від 0,005 до 0,3 МПа;
- Низького тиску з показниками від 0 до 0,005 Мпа.
Треба відразу сказати, що матеріал, з якого повинна бути зроблена газова труба, залежить не тільки від тиску, а й від багатьох інших факторів. Строго кажучи, від тиску взагалі мало, що залежить, тому що сучасна промисловість випускає навіть пластикові труби, здатні за цим параметром конкурувати з металевими.
У загальному випадку газові труби на ділянці можуть бути обрані, виходячи з таких факторів:
- Обстановка населеного пункту;
- Характеристики грунту;
- Агресивність блукаючих струмів і багато інших.
Які бувають труби
Тепер, знаючи, які можуть бути системи газопостачання, слід перейти до розгляду окремих їх складових - труб. Газові труби раніше були представлені тільки одним матеріалом - сталлю. Сьогодні, як уже було зазначено, промисловість випускає і поліетиленові газові труби. При цьому за своїми експлуатаційними характеристиками вони мало чим поступаються металевим.
Огляд поліетиленових виробів
Газові труби на ділянці, зроблені з пластику, характеризуються високим ступенем стійкості до різних атмосферних опадів. Крім того, в хімічному плані вони теж показують відмінну стійкість.
Вироби для дому з пластику досить міцні. Тому з легкістю можуть бути використані на відкритих ділянках і навіть у дуже суворих кліматичних умовах. Здатні зберігати всі свої позитивні якості навіть при дуже низьких температур - аж до -60 градусів.
Ще одним великим гідністю пластика можна вважати те, що йому не страшні блукаючі струми, так як сам по собі поліетилен провідником не є.
Крім усього іншого потрібно відзначити і те, що всі труби з поліетилену не потребують будь-якої додаткової захисту, так як не бояться вологи, на відміну від сталевих виробів.
Ще одним важливим достоїнством можна назвати вартість. Вона практично не відрізняється від вартості сталевих виробів.
Важливо! При всіх таких позитивних якостях в самому будинку рекомендована прокладка тільки металевих труб, а ось в грунт можна класти і поліетиленові.
У загальному сенсі обмеження щодо використання даних виробів наступні:
- Не рекомендується використовувати поліетилен в районах, де температура може опускатися нижче 45 градусів;
- Не можна укладати пластикові вироби в тих районах, де сейсмічна активність може досягати більше 6 балів;
- Так само пластик не використовується в межах міста, де основний газопровід відноситься до першої або другої категорії, тобто має дуже великий тиск;
- Чи не застосовують такі вироби і для пристрою трубопроводів під землею і на землі, а також всередині будинку, як уже було сказано, всередині тунелів і колекторів.
У всіх цих випадках можливе використання тільки сталевих труб.
сталеві вироби
Відразу варто сказати, що всі матеріали зі сталі підлягають електрохімічної і антикорозійного обробці. Це дозволить істотно збільшити термін їх експлуатації. За рахунок цього, вартість всієї конструкції значно збільшується, в порівнянні з вартістю конструкції з пластикових елементів.
Треба сказати, що подібні матеріали мають свою власну класифікацію, так як випускаються вже дуже довгий час. В першу чергу поділ на типи здійснюється за наявністю зварних швів:
- зварні;
- Безшовні.
Всі подібні матеріали можуть бути виготовлені із суміші низьковуглецевої сталі і конструкційної високоякісної сталі. Крім усього іншого, присутні такі добавки:
- Сірка, близько 0,056%;
- Фосфор, порядку 0,25%;
- Вуглець, близько 0,046%.
ГОСТом встановлено, що стінка повинна мати мінімальну товщину близько 3 мм, якщо мова йде про матеріали, які призначені для ведення підземних робіт, і не менше 2 мм для тих матеріалів, які призначені для наземних робота, або непростих завдань у домі.
З цієї точки зору можна виділити наступні важливі характеристики:
- Товщина стінки;
- Діаметр умовного проходу;
- Діаметр газової труби або сума перших двох параметрів.
Отже, сталеві труби, як і пластикові, в залежності від витримується тиску можуть ділитися на три категорії:
- Для укладання під грунтом з робочим тиском до 1,2 МПа. При цьому температура зовнішнього повітря може досягати -30 градусів;
- Для робіт над грунтом з робочим тиском до 1,2 МПа. При цьому температура зовнішнього повітря не повинна бути нижче -10 градусів;
- Для укладання всередині будинку з робочим тиском до 0,3 МПа. При цьому зовнішній діаметр таких виробів не перевищує 15,9 см. Товщина стінок становить близько 5 мм. Температура вироби в процесі експлуатації не повинна бути нижче 0 градусів.
Треба відзначити, що всі газові труби обов'язково повинні пройти антикорозійну обробку. У більшості випадків така обробка полягає у фарбуванні в характерний яскраво жовтий колір.