Related Articles:
Welding is one of the most reliable and common connection methods when laying or repairing plastic pipelines. Welding machine polyethylene pipes it’s easy to master, the main thing is to choose the right type of unit. The main principle of operation of such an installation is to heat the joined sections of pipes and fittings to a viscous flow state and their subsequent connection. When melted, the polymer parts mix with each other and turn into a monolithic compound. A seam is formed at the place of welding, however, it is worth noting that even at joints, correctly welded plastic is not inferior in strength to initially integral sections.
The choice of equipment for thermoplastic pipes depends mainly on what work is to be performed. Of great importance is the diameter of the pipes, the estimated scope of work and the purpose of the pipeline.
The classification of welding equipment is quite diverse and based on various parameters. The main ones are as follows:
- welding method;
- dimensions;
- pipe sizes;
- the presence or absence of a logging function;
- manual or automatic control;
- type of drive.
Butt welding machines
The machine for butt welding of polyethylene is suitable for pipes of various diameters, so when choosing this technique, pay attention to the details of the specification of a particular unit. When butt welding, pipes are fixed in the holders, their ends are heated with the help of a heating element and then are connected to each other under pressure until they are completely cooled. Pipes with a width of 315 mm and more are connected exclusively by the butt method, while the wall thickness of the pipeline should be at least 5 mm, regardless of diameter.
Manual butt welding machines
The larger the pipe, the more difficult the device must be for welding it. Pipes of small diameter in the range of 40-125 mm, as a rule, are connected using a manual device.
Stepan Bykov, expert
Separate manual models allow working with pipes up to 300 mm wide. This unit is compact, easy to use and is often used at home. The main elements of the manual equipment are a centralizer for aligning the connected products, a trimming tool for trimming pipes and a heating plate.

Mechanical butt welding machines
Machines with a mechanical drive are used for welding polyethylene pipes with a diameter of up to 250 mm to create a pressure pipe low pressure. In the event that a pressureless system is laid, the diameter can be increased to 315 mm. Such machines are suitable for welding both at the installation site and in workshop conditions. They are valued for the relatively low weight of the installation itself and its reliability. A number of manufacturers offer mechanical welding equipment with the function of creating plastic bends.
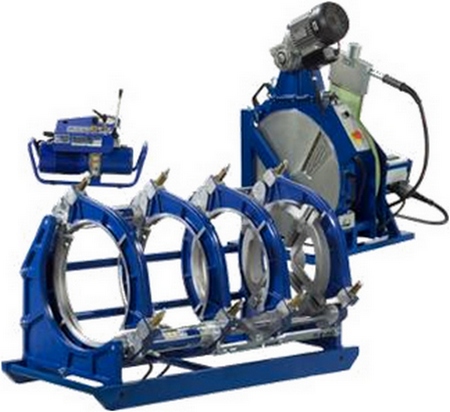
Hydraulic butt welding machines
The centralizer of this type of welding machine is equipped with a hydraulic drive, which allows you to connect pipes of any diameter - from the smallest, 40 mm, to 2000 mm. However, pipes of two meters in width are not capable of welding all devices, the most common upper boundary is 1600 mm.
According to the degree of automation, hydraulic units are divided into 3 groups:
- hand held;
- semi-automatic;
- automatic.
Manual hydraulic apparatus
The main scope of use of handheld devices is laying and installation pipeline systems low or medium pressure. The hydraulic drive and the temperature of the heating element are controlled manually, parameters are selected and set by the operator in accordance with the welding tables. Logging functions of such units are not.

Semi-automatic hydraulic apparatus
These are butt welding machines of medium degree of automation, which are mainly used for medium and large diameter pipes. Semi-automatic installations for welding polyethylene pipes are equipped with an electronic unit that takes the data of the temperature of the welding plate and the oil pressure in the drive, compares their indicators with a given program and, in accordance with the results, sends signals to the operator using the display. Upon completion of the process, a welding protocol is issued. Some semi-automatic units are initially sold without a logging module, however, they can be connected if necessary.

Automatic hydraulic apparatus
Represent the most modern and technological category of welding equipment. The whole process is fully automated and is controlled by an electronic SUVI or CNC module. The operator of such a device only needs to enter the data of the connected products - the material from which the pipes are made, their diameter and SDR. After that, the machine independently selects the optimal welding mode taking into account the air temperature. The apparatus also carries out all cycles of the welding process independently; the final phase is the issuance of a welding protocol indicating all parameters.
Automation of welding eliminates accidental errors typical of manual installations and ensures extremely high quality seams. First of all, automatic devices are used for gas, oil pipelines and other high-pressure systems, the reliability requirements of which are the most stringent.
Electrofusion welding equipment
Welding with the help of electrofusion couplings (fittings with embedded heaters) is carried out using special machines for welding polyethylene pipes. To connect the ends of the pipes, a shaped part is used - a coupling - into which pipes are inserted from both ends. Heating is carried out by electric current. From the apparatus, it is fed to the spirals of the coupling, from which the plastic is heated. Upon reaching the viscous flow state of the material, melting of the part and pipes and their subsequent connection begins.
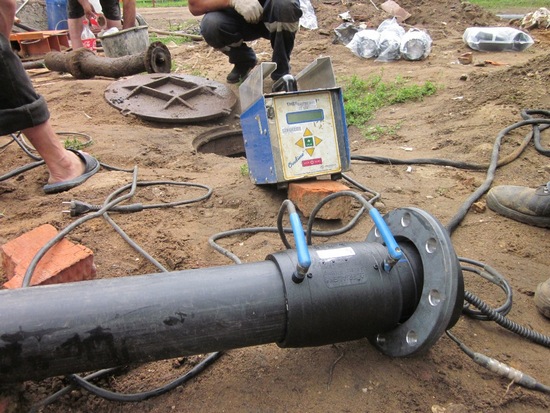
Electrofusion welding is most widely used in the installation of pressure pipelines of small diameter up to 160 mm, pressureless - up to 315 mm. There are also devices for welding polyethylene pipes with couplings, designed for large diameters - up to 630 and even 1600 mm.
This method is also indispensable in those cases when it is necessary to connect multi-meter pipes made of thermoplastic, rolled into bays. Often welding with couplings is also used in the repair of pipelines, since the compact apparatus is easy to use in hard-to-reach areas, as well as in cases where pipes run through a trench or wall.
Another plus is that you can work on electrofusion equipment both in cold weather and in hot weather. The range of operating temperatures is extremely wide, its boundaries are from -20Сº to + 50Сº.
Devices for welding fittings are manual and automatic.
Manual devices for electrofusion welding
When operating plants of this type, the parameters of voltage and welding time are entered directly by the operator. Manual welding machines do not have a function for logging workflow data.
Automatic devices for electrofusion welding
Such devices read information from the barcode of an electrofusion coupling using a special scanner. Having received the data, the unit itself calculates and sets the welding parameters for each connecting part, storing them in the memory block. Depending on the configuration of the model, the operating data of the protocol is either printed out by the output devices in place, or they can be saved on a USB stick and then transferred to a computer.
Choosing an electrofusion welding machine, it is necessary to take into account the cost of fittings. If the pipeline has a considerable length and the nature of the work involves a large number of joints, then it will be more rational to use butt welding and the corresponding equipment.
Crucial in choosing the type of apparatus for welding is the diameter and purpose of the pipeline. Based on this principle, we can find the optimal model, suitable both in terms of its functionality and technical specifications, and at a cost. Welding equipment for working with polyethylene pipes is produced by domestic and foreign manufacturers.
Polyethylene pipes have many advantages. Tolerance of corrosion, chemical resistance, lack of overgrowing of the inner surface, long service life, environmental friendliness. An important advantage is that, due to its rheological properties, polyethylene is a well-welded material - due to the wide temperature range of the viscous flow state of more than 70 ° C) and low melt viscosity.
There are two main methods for the permanent connection of polyethylene pipes - using fittings with embedded heating elements (electrofusion joints) and the butt welding method.
Electrofusion welding of PE pipes
At cost, electrofusion is more costly than butt. This is due to the need to use relatively expensive fittings with built-in heating elements. However, couplings have their own advantages. If the welding of PE pipes is carried out in cramped conditions, in which it is impossible to work with a butt welding machine, the electrofusion method, which does not require a large space, becomes the only alternative.
The essence of electrofusion welding is that the fitting (coupling) with the embedded heater is put on the joint that needs to be welded, and using a special apparatus, voltage is applied to the heating element. When heated, the latter melts the contacting surfaces of the coupling and the pipeline, resulting in a tight joint. Compact and lightweight devices for socket welding are convenient to use and consume little power.
Butt welding of PE pipes
This method is the most versatile and in demand when creating one-piece joints. Strength butt welds not inferior to the strength of neighboring sections, and the welded pipeline in terms of tightness, flexibility and reliability is no different from a whole pipe.
Butt joint performed in the following sequence:
- installation of the ends of the pipes to be welded into the coupling welding machine, their alignment and fixation;
- milling and machining of the ends with the help of a miter;
- installation between the welded ends of the mirror, heating and fusion of the ends pressed to the device;
- removing the mirror from the work area;
- pressing the molten ends to each other with a certain force and keeping them under pressure until the connection is cooled.
When controlling the quality of welding, they are guided by the shape and dimensions of the formed burr (rollers around the joint). Its geometric parameters must meet certain requirements. The quality of work depends not only on the correct selection of welding equipment, but also on the degree of qualification of the welder.
The characteristics of the welding machines used depend on the diameters of the pipes being welded and the degree of automation of the work. The necessary equipment can be selected in the section “Butt welding machines”.